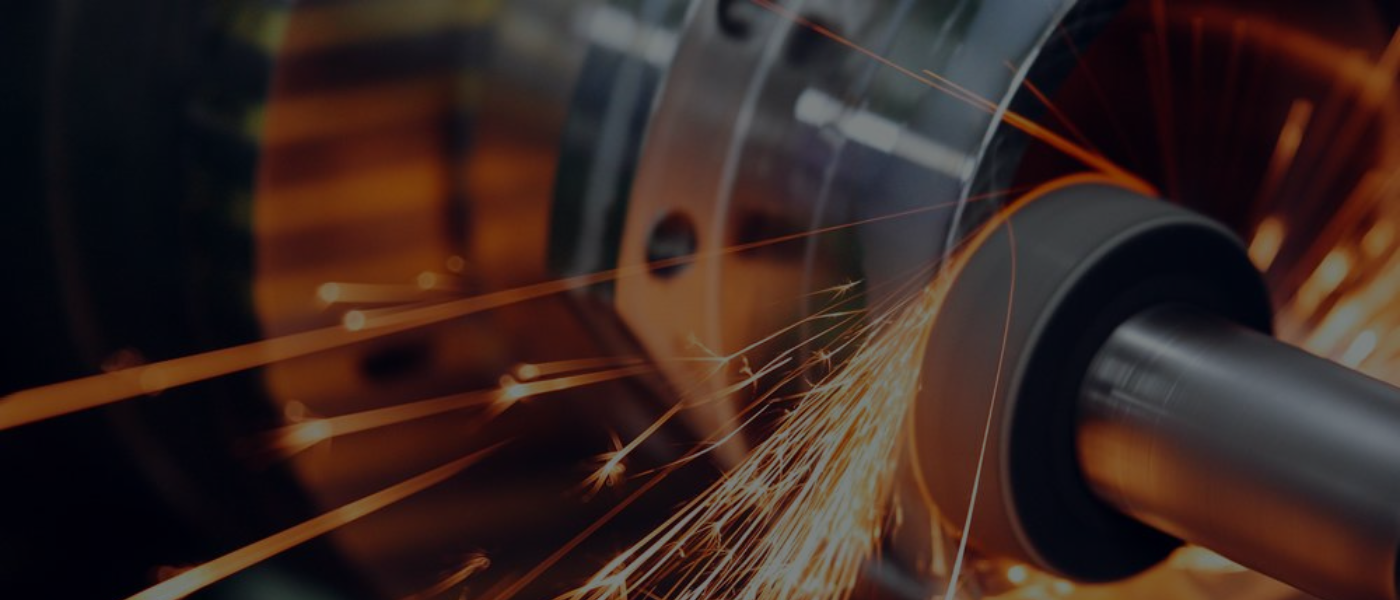
Retos sector metal
Retos del sector metal: Conócelos El sector del metal sigue siendo crucial para la economía española, cuyas empresas conforman una parte muy importante del tejido industrial. Pero ¿cómo se presenta el futuro? En este nuevo artículo vamos a abordar los principales desafíos a los que este tipo de empresas se enfrentan y las soluciones que se atisban en el horizonte. ¡No te las pierdas! Índice A qué desafíos se enfrenta la industria del metal A continuación, te desglosamos los 9 grandes retos del sector metal a los que todas las empresas se enfrentarán en los próximos años. 1. Costes reales de producto por orden de fabricación Comenzamos por un desafío que se antoja casi obligatorio. Se trata de realizar un seguimiento preciso de los gastos involucrados en cada eslabón de la empresa. Esto tiene una importancia capital a nivel de negocio porque es lo que dibujará la realidad de costes, pérdidas y beneficios, para a continuación aplicar soluciones específicas. 2. Control y ejecución de mermas Siguiendo con el punto anterior, las mermas suponen una pérdida económica muy importante para las empresas del metal. Poner en marcha sistemas de control efectivos es fundamental para reducirlas. Aquí entran en juego la automatización y el análisis de cada proceso para lograr optimizarlos. 3. Gestión total de la trazabilidad Asegurar la trazabilidad total en la industria del metal será otro de los pilares para cumplir con las normativas y mantener la confianza de los clientes. Un sistema de trazabilidad permite seguir el recorrido de cada pieza desde su origen hasta su destino final, así como la rápida localización de fallos en la cadena de producción. 4. Mejora en la logística interna y cadena de valor Una gestión eficiente de la cadena de valor permite identificar cuellos de botella, sincronizar etapas de producción y reducir los costes operativos. Al mejorar la logística interna, las empresas del sector del metal pueden incrementar su capacidad de respuesta y su competitividad en el mercado. 5. Eliminar papel La eliminación del papel en la gestión de procesos es un paso importante hacia la digitalización completa. El hecho de pasar de registros manuales a soluciones digitales mejora la precisión de los datos, facilita el acceso a la información en tiempo real y permite una toma de decisiones más rápida, justo lo que planteamos con nuestra herramienta. 6. Control total de la producción Las empresas del sector del metal deben contar con sistemas que les permitan monitorizar en tiempo real todas las fases de su proceso productivo. Esto incluye desde la planificación hasta la entrega, garantizando que se cumplan los estándares de calidad y los plazos de entrega acordados con los clientes. 7. APQP y auditorías digitales Las auditorías digitales y el uso de APQP son esenciales para cumplir con las normativas internacionales como IATF e ISO 9001. Estas herramientas permiten asegurar la calidad desde las primeras etapas del diseño del producto. Además, proporcionan una trazabilidad completa en las auditorías, facilitando la mejora continua y asegurando que se cumplen los requisitos normativos. 8. Planificación de la producción Una correcta planificación de la producción se deberá tener en cuenta para evitar retrasos y maximizar la eficiencia. Para ello será necesario gestionar el equilibrio entre la demanda y los recursos disponibles. Los softwares de gestión, como MESbook, ayudan en buen grado a esto, mejorando la capacidad de respuesta ante cambios y evitando ineficiencias en la cadena de producción. 9. Cuadros de mando específicos de situación y control Por último, los cuadros de mando son herramientas estratégicas que permiten visualizar de manera clara el estado de los procesos productivos. Estos paneles integran información clave para facilitar la toma de decisiones basadas en datos. En el sector del metal, contar con un cuadro de mando adecuado permite a los responsables identificar problemas, evaluar el rendimiento y ajustar rápidamente los recursos en función de las necesidades operativas. Cómo solventar estos retos Todo este paradigma lleva a una misma piedra angular: la digitalización y el control de procesos a nivel industrial. Solo de esta manera las empresas del sector del metal serán capaces de afrontar estos desafíos con solvencia. Programas específicos de gestión, como MESbook, permiten aglutinar todos los datos procedentes de los distintos puntos de la cadena de proceso, interpretarlos y mostrarlos de una forma fácil de comprender. De este modo, los responsables podrán tomar decisiones de una forma más sencilla, meditada y segura para optimizar el rendimiento global. Y esto no solo incluye los aspectos puramente técnicos, sino también los económicos o los relativos al personal, por citar algunos. Este tipo de soluciones se combinan a la perfección con dispositivos y herramientas derivadas del IoT o la IA, generando un salto de gestión nunca visto, a la par que necesario, en el sector. Si tú también quieres adaptar tu empresa para afrontar los grandes retos que están por venir, te invitamos a conocer en mayor profundidad nuestra herramienta. Estaremos encantados de explicarte todo lo que puede hacer por ti. Ingeniero comercial en MESbook Jose Antonio Nigro