La merma es el porcentaje o cantidad de pérdida o ganancia (de producto, energía, dinero…) en cada etapa del proceso de producción como desviación respecto del consumo esperado de cada material utilizado para la fabricación de un producto. Para hacer un correcto control de la merma y reducirla, es necesario planificar la producción adecuadamente y medir las pérdidas o ganancias en cada etapa.
De esta forma, podemos cuantificar el coste de las pérdidas o ahorros y determinar las causas más frecuentes, incluyendo caducidad, rotura, sobreproducción, procesamiento inadecuado, error administrativo y robo. Además, la reducción de la merma también contribuye a la protección ambiental y a un uso más responsable y sostenible de los recursos naturales.
En qué consiste la merma y qué la produce
La merma en producción se refiere generalmente a la pérdida o disminución de materiales, insumos, productos o recursos que se generan durante el proceso de producción y puede incluir el robo o un coste energético innecesario. También puede existir una ganancia de merma cuando producimos un producto utilizando menos recursos materiales que los definidos como estándar en el sistema
Cuando una empresa produce bienes, es común que se generen desperdicios debido a diferentes factores como errores humanos, fallas técnicas, mal uso de maquinarias, tiempos de espera, errores en la definición de estándares, entre otros.
Esta merma puede ser de diversos tipos, desde materiales en el proceso de manufactura, la disminución de productos derivados a partir de una materia prima, hasta la pérdida de energía durante el proceso de fabricación.
Una empresa debe tener en cuenta la cantidad y tipos de merma que se generan en su proceso productivo, ya que éstos afectan significativamente a los costos de producción, calidad de los productos y el rendimiento económico de la organización. Es importante identificar y medir la merma para poder tomar medidas preventivas y correctivas, como la optimización de la eficiencia de los procesos, el mejoramiento de los sistemas productivos y el reciclado de los desperdicios para evitar su impacto negativo en el medio ambiente. Nos ayuda también a detectar errores en la creación de las listas de materiales u hojas de ruta saber detectar los motivos de pérdida.
La merma en producción puede tener diversas causas:
- Una de ellas es la mala planificación de la producción, lo que puede derivar en un exceso o déficit de la misma.
- La falta de mantenimiento adecuado de las maquinarias puede provocar fallos y detener la producción.
- También influyen los errores humanos en el proceso, como la falta de capacitación o el incumplimiento de las medidas de seguridad.
- Los errores en el diseño de los productos o en la atención al cliente pueden causar problemas en la producción y disminución en la demanda.
- Problemas de maquinaria o recursos energéticos. Es decir, un coste o acción excesivo, desproporcionado e innecesario.
- Errores en la definición de los estándares de las listas de materiales u hojas de ruta
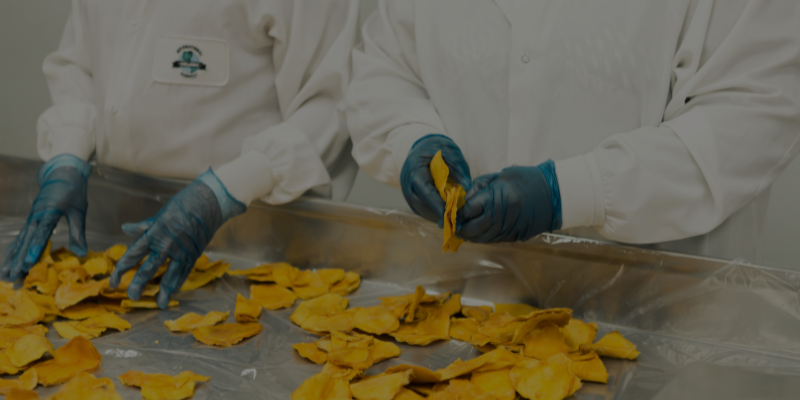
Cómo se controla la merma en las fábricas alimentarias
La merma en una fábrica alimentaria es aquella cantidad de materia prima o producto final que se pierde durante el proceso productivo. Para el control de la merma en producción y evitar pérdidas económicas, es importante implementar medidas de prevención y control.
Una de las primeras medidas es llevar un registro exhaustivo de la cantidad de materia prima utilizada y de los productos finales obtenidos. Esto permitirá identificar de forma precisa las áreas donde se producen las mayores pérdidas y tomar medidas a tiempo.
Otro aspecto clave es garantizar una correcta gestión del almacenamiento y la conservación de la materia prima y los productos. Para ello, es fundamental seguir las especificaciones del fabricante y establecer un sistema de control de stock.
También se puede reducir la merma con una adecuada planificación de la producción, evitando la sobreproducción, y optimizando los procesos de envasado y etiquetado, entre otros.
Por último, es importante sensibilizar al equipo de trabajo sobre la importancia de controlar la merma y fomentar una cultura de prevención y mejora continua.
Cómo reducir las mermas en producción
Las mermas en producción se pueden reducir de varias formas. Una de las formas más efectivas es optimizando los procesos de producción y logística. Esto se logra mediante la implementación de un sistema de gestión de los procesos que permita tener un control sobre los insumos, los procesos y los productos terminados.
También se pueden utilizar métodos de análisis de desempeño para identificar los puntos de mejora en los procesos.
Otra de las estrategias es implementar un sistema de administración de inventarios efectivo, que permita optimizar los niveles de inventario y minimizar las sobras. Además, es importante evaluar la demanda de los productos y ajustar la producción de acuerdo a la misma, para evitar excedentes.
Por último, se pueden optimizar las prácticas y procesos de manejo y almacenamiento de los materiales y productos, de manera que se minimicen las pérdidas por deterioro o caducidad.
Todo lo anterior, permitirá reducir las mermas en la producción y obtener un mejor rendimiento de los recursos utilizados, lo que se traducirá en beneficios para la empresa y en un menor impacto ambiental.
Tipos de mermas
Las mermas son parte del proceso de producción en cualquier empresa, y se refieren a la cantidad de material o producto que se pierde o gana durante este proceso debido a problemas de calidad y desperdicios o errores en los estándares. Hay varios tipos de mermas en producción, aquí te mencionaré algunos de los más comunes:
- Mermas de producción: son aquellas que se dan durante la fabricación de un producto, como por ejemplo, la sobrante de materiales después de un corte. Estas pueden ser clasificadas como mermas de proceso o mermas de material.
- Mermas de almacenamiento: estas ocurren cuando un producto o material está almacenado y se deteriora o se daña durante el periodo de almacenamiento, ya sea por falta de control de temperatura, humedad, luz, etc.
- Mermas de transporte: es la cantidad de producto o material que se pierde durante el traslado de un lugar a otro, ya sea por daños durante el transporte o por pérdida durante el mismo.
- Mermas de calidad: estas son las mermas que se originan por desperfectos o defectos en los productos que se fabrican. Por ejemplo, productos que no pasan los estándares de calidad establecidos por la empresa, que no están en las condiciones adecuadas de empacado y etiquetado, etc.
- Mermas por errores en los estándares. No es poco frecuente que se generen errores a la hora de la definición de los estándares de materiales, lo que provoca graves problemas de desajuste de stock. Es bastante difícil detectarlo antes de llegar a la rotura de stock. Por lo que es imprescindible controlar el consumo en tiempo real durante el proceso productivo.
En conclusión, es esencial que las empresas realicen una adecuada gestión y un buen control de las mermas en producción, ya que esto puede impactar significativamente en la rentabilidad del negocio. Por eso, es importante implementar medidas para evitar o disminuir las mermas, lo cual puede incluir mejoras en los procesos de producción, en la calidad de los materiales y productos, en el control de almacenamiento y transporte, entre otras.

Adjunto a Dirección Comercial en MESbook.
Arturo Torres
Ingeniero industrial con más de 27 años de experiencia en distintos sectores como director de operaciones, Supply Chain, Procesos y Calidad. Docente en instituciones como la Cámara de Comercio y el Consejo General de la Ingeniería Técnica Industrial de España.