GESTIÓN DE PRODUCCIÓN OEE
Productividad de la fábrica en tiempo real
Con MESbok gestionas las causas de OEE y de NO OEE.
Qué es el OEE en producción
El OEE (Overall Equipment Effectiveness) es el indicador estándar para medir la productividad de la fabricación identificando el tiempo de fabricación que es realmente productivo.
El Indicador OEE es el punto de partida para la producción 4.0, es decir, tener en el día a día de la fábrica todo lo que se requiere para fabricar y tener un sistema de gestión de producción eficaz:
- Documentación y procedimientos
- Avance de órdenes en tiempo real y en automático
- Detección de ineficiencias
- Rutinas de trabajo como cambios de turnos, inicio de día, etc.
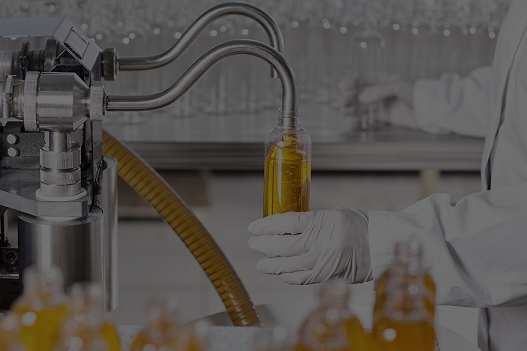
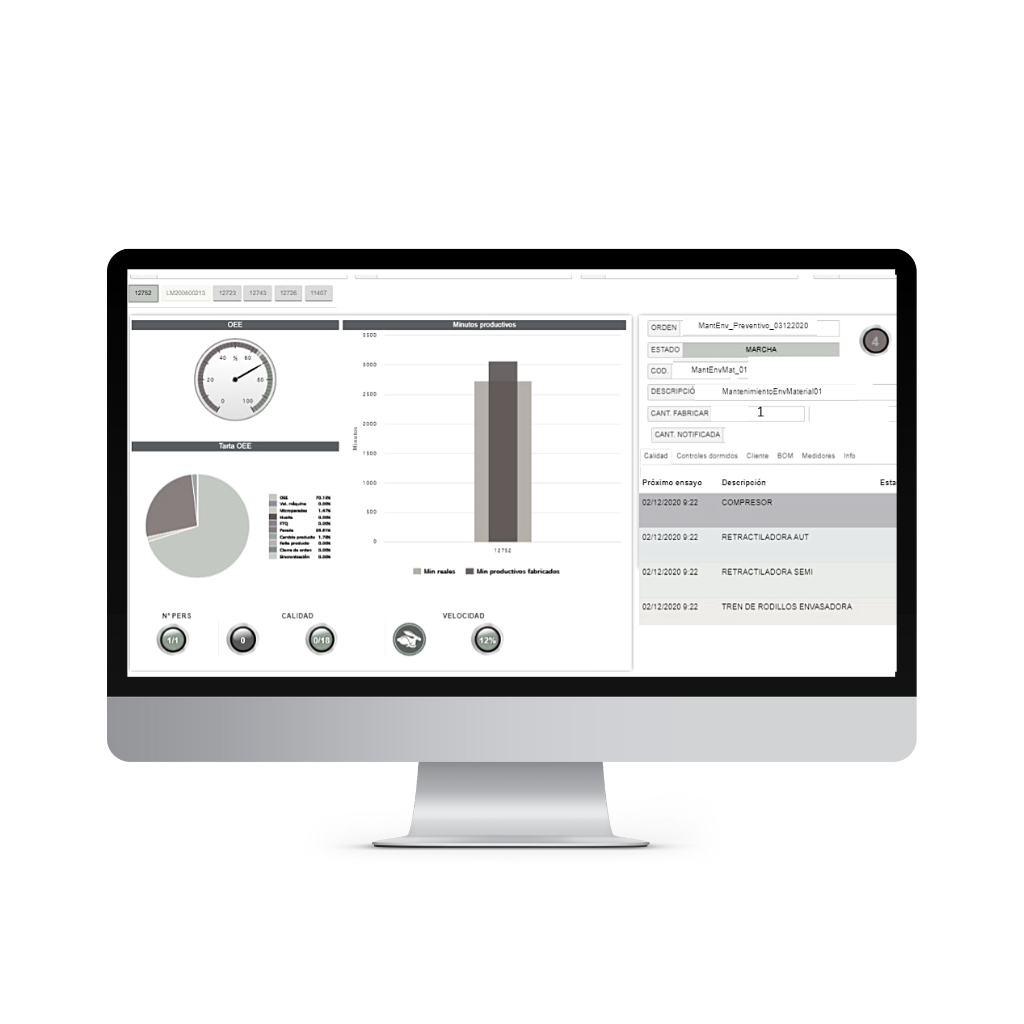
Cómo mejorar la eficiencia productiva con MESbook
- Automatización de procesos de captación, procesamiento y análisis de datos de Producción, Productividad, Calidad, Almacén y Mantenimiento.
- Gestión de Fábrica en Tiempo Real con Sistema MES
- Paper Free Manufacturing
- Centralización de toda la documentación relevante de métodos de fabricación, fichas de producto, instrucciones de cualquier tip para que exista un único acceso para el personal.
- Detección de ineficiencias
- LEAN 4.0 – Proyectos DMAIC
Ventajas del indicador OEE
Identifica la fábrica oculta, las causas de NO OEE
La forma más sencilla de calcular el OEE es la relación entre el tiempo productivo total y el tiempo de producción planificado. El Tiempo Totalmente Productivo es otra forma de decir que sólo se fabrican piezas buenas lo más rápido posible (Tiempo de Ciclo Ideal) sin tiempo de parada.
El OEE es necesario pero no suficiente, pues no proporciona información sobre los factores relacionados con las pérdidas productividad en una fábrica.
Decimos en MESbook que el OEE es una condición necesaria, pero claramente insuficiente. El siguiente paso debe ser identificar las causas de NO OEE como son: la Velocidad, Calidad, Averías, Microparadas, Falta de Producto y Cambio de Producto.
PREGUNTAS FRECUENTES
Es importante medir el OEE (Overall Equipment Effectiveness) de una fábrica porque proporciona una visión clara y objetiva de la eficiencia de la producción. El OEE mide la capacidad de las máquinas y equipos para producir productos de calidad en el tiempo y cantidad adecuados, y se utiliza para identificar oportunidades de mejora en los procesos de producción.
Si una fábrica no mide su OEE, puede haber una serie de consecuencias negativas, como la falta de visibilidad sobre el rendimiento de la producción, la incapacidad para identificar cuellos de botella y la pérdida de oportunidades para mejorar la eficiencia y reducir costos. Además, sin medir el OEE, es difícil establecer objetivos de producción realistas y tomar decisiones informadas sobre la inversión en nuevos equipos y tecnologías.
Para identificar las causas de un bajo OEE, un sistema MES puede monitorear los tiempos de parada de la maquinaria, los tiempos de inactividad, los tiempos de ciclo y otros datos clave de producción. Conectándonos con las maquinas mediante sistemas de PLC, OPC, etc.
Estos datos se pueden utilizar para identificar cuellos de botella, ineficiencias en los procesos y otros problemas que estén afectando el rendimiento de la producción.
Además, un sistema MES puede realizar un seguimiento de los problemas de calidad y de las piezas defectuosas producidas, lo que puede ser una causa importante de un bajo OEE. Al identificar los problemas de calidad y las piezas defectuosas, se pueden tomar medidas para mejorar los procesos de producción y reducir los tiempos de inactividad asociados con la producción de productos no conformes.
Por avisos que indican que la línea/ máquina está en paro en ese momento. Estos se recogen en tiempo real y dependiendo de la señal se identifican automáticamente o se avisa al operador para su identificación, pudiendo llegar hasta 2 niveles de no OEE. También permite analizar esas causas de fallos y no OEE y realizar planes de mejora para minimizarlos.
Los módulos de Mesbook se puede contratar de forma independiente, aunque están vinculados de forma nativa entre todos.
¿Estás interesado en conocer más?
Ponte en contacto con nosotros y te contaremos cómo podemos ayudarte