La gestión de turnos de trabajo siempre es una complicación para las empresas, y más aún para las fábricas. Hacerlos de forma correcta o encontrar la fórmula definitiva no es sencillo y a menudo existen numerosos intentos fallidos de gestión de turnos en fábricas lideradas por administrativos que no cuentan con un software de RRHH para la industria.
Requisitos para que sea necesario organizar turnos laborales
A pesar de ello, no hay unos requisitos concretos para que sea necesario organizar turnos laborales, pues las simples diferencias entre trabajadores, sus especialidades, capacidades, años de experiencia y también las propias particularidades del día a día en la fábrica hacen necesario el diseño de unos turnos laborales adaptados. Así como fechas, horas de funcionamiento de la maquinaria, etc.
Con unos turnos bien definidos, coherentes y centrados en la productividad, la eficiencia en producción, el aprovechamiento de los recursos y la satisfacción de empleados y clientes finales, cualquier fábrica podría incrementar su posición en el mercado.
Tipos de turnos de trabajo más habituales en España
En España existen muchos tipos de turnos, por lo que la gestión de turnos en fábricas no debe ser compleja a priori siempre que esta esté estructurada por personas o herramientas profesionales.
Turnos discontinuos
Los turnos discontinuos hacen referencia a las horas en las que la compañía o fábrica es productiva y se encuentra disponible para la atención al cliente, por ejemplo. Y por supuesto, está vinculada a los horarios de los trabajadores.
Los turnos discontinuos son los más comunes en España y muchos otros países. Consisten en turnos de mañana y tarde con algunas horas o solo minutos de descanso usualmente a la hora del almuerzo.
Este tipo de turnos incluyen fines de semana de descanso. Es decir, que no existe actividad laboral durante el sábado y el domingo.
Turnos semidiscontinuos
Los turnos semidiscontinuos incluyen horas de productividad y trabajo tanto en la mañana como en la tarde y la noche. Sin embargo, también suelen existir algunos descansos, por ejemplo, entre la mañana y la tarde, también a la hora del almuerzo, mientras que la tarde y la noche no presentan pausa intermedia.
Es común que en los turnos discontinuos también se trabaje muchos sábados o casi todos.
Turno continuos
Se le llama turnos continuos cuando una empresa, fábrica, firma… está siempre en funcionamiento. Es decir, cuando en cualquier se está produciendo y existe también la posibilidad de contactar con algún empleado o administrativo de la compañía.
En estas empresas se trabaja todos los días de la semana, del mes y del año, sin excepciones de festivos y horarios.
Los turnos continuos son poco comunes. En ocasiones los ofrecen algunas fábricas, compañías y también supermercados o lugares de primera necesidad como farmacias. Son establecimientos conocidos como 24h o 24/7.
Por supuesto, al igual que en los casos anteriores estos turnos no hacen referencia a los empleados, sino a los de la propia compañía, que tras elegir el horario deberá combinar y gestionar los turnos de los trabajadores para ofrecer una fábrica de turnos discontinuos, semidiscontinuos o continuos.
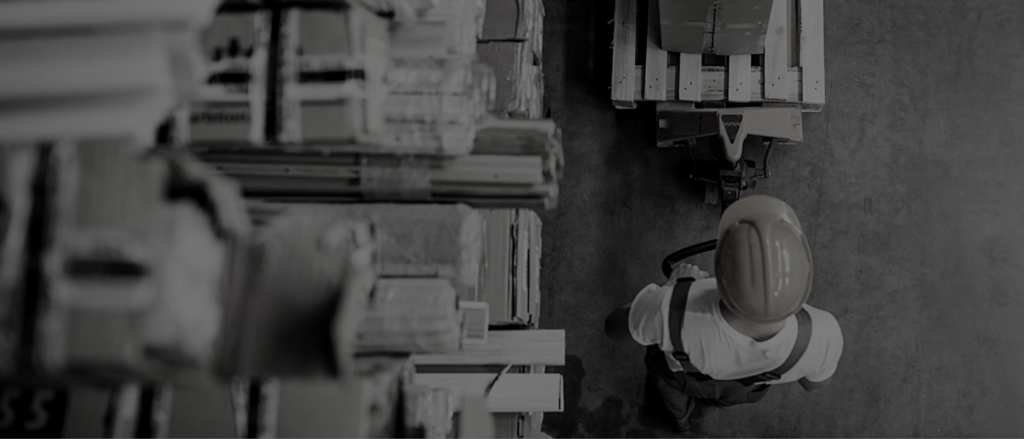
Cómo implementar una gestión de turnos en una fábrica
No hay una única forma de hacer una gestión de turnos en fábricas correcta. De hecho, cada fábrica contará con un modelo idóneo al cual podrá llegar tras diferentes cálculos y ajustes que pueden llevar más o menos tiempo y decisiones.
Lo fundamental es tener claro qué elementos se deben tener en cuenta antes de establecer y gestionar los turnos de la fábrica para los empleados.
Son los siguientes:
- Horario de la fábrica.
- Tiempos de inicio y finalización de maquinaria, sistemas, puertas, controles de seguridad…
- Horarios de empleados y sus posibilidades de conciliación.
- Experiencias, capacidad, conocimiento y más aptitudes y actitudes de los empleados en relación con la fábrica, la comunicación dentro de la misma, el funcionamiento de la maquinaria, etcétera.
- Tiempo de funcionamiento de la maquinaria y sus cualidades o necesidades.
- Normativa de la localidad y comunidad en cuanto a la actividad de la fábrica, así como horarios, niveles de ruido…
- Tipos de jornadas de los trabajadores, vacaciones, posibilidades de días propios…
- Horarios, productividad y eficiencia de los transportes y transportistas.
- Tiempos necesarios para la fabricación, el packaging, la gestión y administración, el transporte.
- Los tiempos y movilidad del stock.
- Y más.
Los aspectos que se deben tener en cuenta son casi inabarcables. Por ello, Recursos Humanos y otros departamentos deben trabajar en conjunto para formular diferentes pruebas e incluso simulaciones con la finalidad de conocer cuál será la más correcta gestión de turnos en las fábricas. Así como apoyarse en herramientas profesionales como las que Mesbook pone a su disposición.
Un objetivo fundamental, además, debe ser acabar con las largas jornadas laborales para los trabajadores, pues de forma genérica tienen grandes repercusiones sobre su salud, y en concreto en el entorno de las industrias, existen muchos más riesgos laborales.
Esto perjudica al trabajador y de forma paralela a la propia firma y a los clientes.
Por ello, los turnos rotativos de los empleados son extremadamente populares, si bien no siempre serán adecuados en todas las fábricas.
Algunas de sus bases son:
- No adjudicar el turno nocturno más de dos semanas seguidas al mismo empleado.
- Garantizar seguridad e higiene para todos los empleados, trabajadores, operarios, responsables…
- La opción de incluir empleados turnantes para completar equipos.
Asimismo, es obligatorio que entre jornadas exista al menos un descanso de 12 horas, que solo se podrá reducir a 7 horas en casos muy excepcionales.
También es importante tener en cuenta las opciones y ventajas o inconvenientes que pueden tener los turnos rotativos dobles de mañana y tarde para los empleados. O los rotativos triples de mañana tarde y noche.
Con todas estas variables, opciones y normas es muy complejo llegar a una buena gestión de turnos en fábrica sin tener al alcance de quien tome decisiones toda la información posible.
Sistema para gestión de turnos
Es necesario contar con una herramienta digital para poder controlar todas las variables de manera automática, no solo para los turnos, sino para todo lo que abarca la gestión de los recursos humanos de una fábrica. Además el sistema debe proporcionar el aseguramiento de la normativa, contando con restricciones en tipologías de horas, pluses… según convenio para no sobrepasar los límites estipulados.
Por ello, para no malgastar intentos es conveniente contar con un sistema operativo destinado a la gestión de turnos en fábricas como algunas de las opciones que ofrece el sistema MESbook. Contacta con nosotros.

Product Manager en MESbook
Marta Cejudo
Ingeniera de organización industrial con 4 años de experiencia en gestión de fábricas en tiempo real como KAM.