SISTEMA DE PLANIFICACIÓN DE LA PRODUCCIÓN
Conoce nuestro método de planificación y programación para fábricas
Qué es el software de planificación de la producción
El módulo de planificación y secuenciación de MESbook ayuda a planificar y programar la producción de manera óptima y conectada con la realidad de la planta al trabajar totalmente integrado con MESbook fabricación.
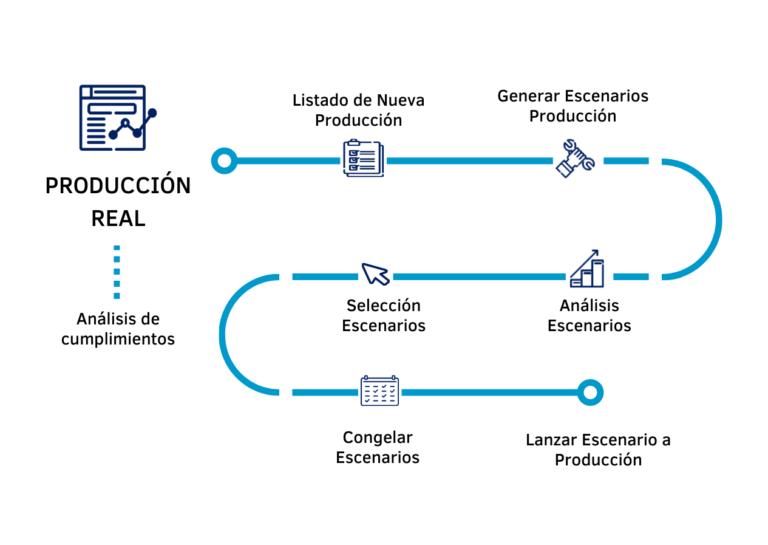
La clave de nuestro método de secuenciación: Servicio y Productividad
Disponibilidad de recursos
Minimizar ineficiencias
Comunicación entre departamentos
Qué incluye el módulo Planificación/ Secuenciación de MESbook
- Secuenciación de la producción a modo de visualización gráfica tipo diagrama de Gantt.
- Horizonte de visualización temporal desde horas a semanas.
- Adecuación a complejidad productiva de rutas simples, redes de rutas y operaciones en paralelo.
- La comunicación con cualquier fuente de datos mediante plataforma de web-api que conecta MESbook con los subsistemas de modo directo.
- Adaptable a diferentes tipos de arquitectura de fábrica: máquinas en serie con sistemas de flujo uniforme o de tipo taller, sistemas de fabricación abierto.
Ventajas del sistema de Planificación y Programación
PROGRAMACIÓN DE LA PRODUCCIÓN
Ayuda a programar la producción teniendo en cuenta las restricciones y recursos físicos finitos disponibles: personas, máquinas y costes.
gestión de programaciones
Proporciona de manera automática, rápida y sin errores, diferentes escenarios para la gestión de las programaciones sencillas.
SISTEMATIZACIÓN
Sistematiza un proceso clave para la empresa reduciendo dependencia de personas, hojas Excel, etc.
FIABILIDAD
Se comunica y retroalimenta de forma bi-direccional con el módulo de producción de MESbook, mejorando la fiabilidad al trabajar siempre con la realidad de la fábrica.
Nos adaptamos a cada necesidad
Niveles de planificación y programación
planificador básico
- Ordenación lógica de OF, agrupadas con criterios y visualización de tiempo previsto de finalización.
- Visualización gráfica a modo de diagrama de Gantt de órdenes y recursos.
- Manejo de interface gráfico “drag&drop” asignando las ordenes a las líneas con recalculo de tiempo estimado de finalización calculado a velocidad estándar.
- Conectividad: Conectado al Plan de Producción del ERP y a la fabricación real (procesadas y buenas si hay rechazo automático) y al ERP a efectos de buenas dadas de alta en el sistema.
- Capacidad finita.
- Planificación por lotes y en serie.
- Sistema de alertas personalizable.
planificador secuenciador inteligente
- Incorpora al planificador una propuesta de secuencia óptima en base a plazos solicitados, matriz de cambios y criterios de disponibilidad de recursos (personas y máquinas) y costes.
- Escenarios: posibilidad de realización de escenarios y tras la revisión por parte del usuario, este podrá decidir cuál de todos los escenarios pasa a ser el actual de forma que todos los datos se actualicen.
- Flexibilidad para el tratamiento de las tareas: dependencias, división de tareas encadenadas o en paralelo, etc.
- Trabaja con un motor de Machine Learning y aplicando Inteligencia Artificial propone las mejores secuencias y escenarios productivos.
- Tiene en cuenta los recursos alimentados en la herramienta.
Beneficios de incorporar nuestro módulo en las fábricas
Mejora del servicio al cliente
Maximiza la productividad
Minimiza los costes de fabricación
Mejora la coordinación interna
- Trabajar en maximizar la productividad desde antes de producir.
- Asegurar una planificación factible con una fecha de finalización fiable.
- Fabricar en función de opciones configurables por la empresa.
- Mejorar la coordinación entre producción, compras y comercial.
- Conocer de antemano lo que estará retrasado para coordinar con el cliente.
- Tener flexibilidad para ajustarse a cambios en la demanda.
- Planificar diferentes escenarios de planificación para elegir el mejor en cada momento.
- Poder replanificar la producción inmediata ante problemas internos (rotura de una máquina, no disponibilidad de una materia prima, etc.)
- Poder planificar acciones de mejora y mantenimiento con antelación en periodos de baja actividad, sin que afecte a la producción.
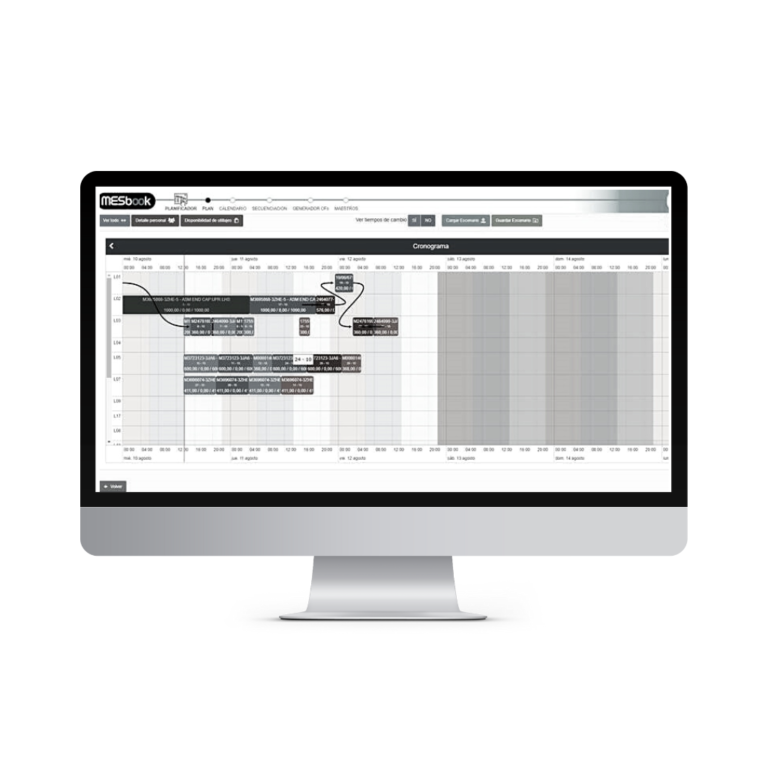
PREGUNTAS FRECUENTES
La restricción de capacidades se refiere a la limitación de la producción de una planta debido a la capacidad limitada de un activo o recurso. Esto puede ser un cuello de botella en el proceso de producción que impide que se produzca más, lo que puede reducir la eficiencia y aumentar los costos.
Un sistema de programación de producción integrado en un sistema MES puede abordar la restricción de capacidades al permitir la planificación y programación de la producción en función de la capacidad disponible de los recursos, lo que optimiza la utilización de los mismos. Además, el seguimiento en tiempo real de la producción permite ajustar la secuencia de producción en función de la disponibilidad de los recursos y maximizar la eficiencia en tiempo real.
Un sistema de programación de producción integrado en un sistema MES permite el seguimiento en tiempo real de la producción, lo que permite ajustar la secuencia de producción en función de la disponibilidad de los recursos y maximizar la eficiencia en tiempo real. Esto significa que se puede identificar temprano cualquier posible problema y tomar medidas correctivas antes de que se convierta en un problema mayor.
Un sistema de programación de producción integrado en un sistema MES permite la planificación y programación de la producción en tiempo real, lo que permite ajustar la secuencia de producción en función de la disponibilidad de los recursos y maximizar la eficiencia en tiempo real. Además, el seguimiento en tiempo real de la producción permite ajustar la secuencia de producción en función de la disponibilidad de los recursos y maximizar la eficiencia en tiempo real.
¿Estás interesado en el módulo Planificación/Secuenciación?
Contacta con nosotros para solicitar una demo o presupuesto personalizado