La Metodología 5S se centra en la optimización y la organización en la Industria Automotriz. Si deseas descubrir cómo estas cinco «S» pueden revolucionar la producción y la gestión en este sector, estás en el lugar adecuado.
En la competitiva industria automotriz, la eficiencia es clave para mantenerse a la vanguardia. Una de las herramientas más poderosas para lograrlo es este célebre sistema. Acompáñanos en este emocionante viaje para conocer qué es exactamente esta sistemática, cómo se implementa y por qué las principales empresas la han adoptado con éxito.
¿En qué consiste esta metodología?
La Metodología 5S es un sistema de gestión originario de Japón que se enfoca en mejorar la organización y la eficiencia en el lugar de trabajo. Esta herramienta, perteneciente al Lean Manufacturing, define prácticas de mejora en cuanto al orden y la limpieza, al mismo tiempo que establece estándares en procesos eficientes y eficaces. De esta manera, mejora los puestos de trabajo, lo que conlleva a un incremento en la productividad de los procesos industriales.
El nombre «5S» proviene de cinco palabras japonesas, cada una de las cuales representa una etapa fundamental en el proceso de implementación. A continuación, describimos qué significa cada una de estas etapas:
¿Cuáles son las 5S?
- Seiri (Clasificación): Implica la identificación y eliminación de elementos innecesarios en el área de trabajo, como herramientas no utilizadas, piezas defectuosas o equipos obsoletos en cada puesto de trabajo o área donde se aplica la metodología.
- Seiton (Orden): Una vez clasificados los elementos necesarios en el puesto de trabajo, deben organizarse eficientemente. Esto incluye asignar ubicaciones específicas a herramientas y piezas para asegurar que estén fácilmente accesibles y disponibles cuando se necesiten.
- Seiso (Limpieza): La Metodología 5S nos enseña que, para tener un lugar limpio, primero debe estar clasificado y ordenado. Mantener un entorno de trabajo limpio y ordenado no solo aumenta la seguridad, sino que también contribuye a la calidad y precisión de la producción automotriz.
- Seiketsu (Normalización): Esta cuarta etapa se enfoca en establecer estándares y procedimientos para mantener las 5S a largo plazo. El objetivo es crear hábitos y rutinas que formen parte de la cultura organizacional.
- Shitsuke (Disciplina): La quinta y última «S» se refiere a la disciplina necesaria para mantener y mejorar continuamente las 5S. Trabajar con esta metodología genera cultura y motivación en las personas para que comprendan su propósito. Esto implica compromiso, automotivación, constancia y perseverancia de todos los miembros del equipo.
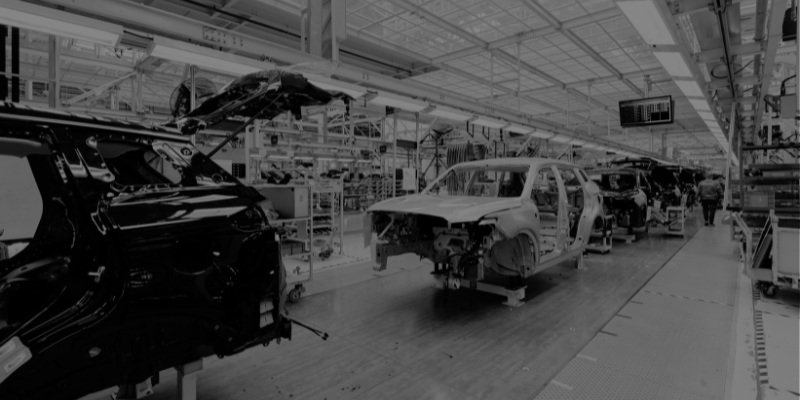
¿Por qué adoptar esta metodología en la Industria Automotriz?
Las empresas de la industria automovilística utilizan la Metodología 5S para mejorar la eficiencia y la calidad en el lugar de trabajo. Algunos beneficios de implementar un sistema de 5S en la industria automotriz son:
Mejora de la eficiencia operativa: Las 5S ayudan a eliminar el desperdicio y la ineficiencia al organizar el lugar de trabajo de manera que las herramientas, piezas y equipos necesarios estén fácilmente identificados y disponibles. Esto reduce los tiempos de búsqueda y mejora la productividad.
Reducción de costos: Al reducir el desperdicio y mejorar la eficiencia, las organizaciones de la industria automotriz pueden reducir los costos operativos, incluyendo los relacionados con el almacenamiento innecesario, la compra de piezas y herramientas duplicadas, y la mala utilización de la mano de obra.
Mejora de la calidad: Las 5S fomentan la estandarización y la consistencia en los procesos, lo que a su vez conduce a una mayor calidad de los productos y a una reducción de los defectos. Al tener un lugar de trabajo limpio y ordenado, se pueden identificar fácilmente problemas y anomalías.
Seguridad mejorada: Un lugar de trabajo organizado y limpio reduce los riesgos de accidentes y lesiones. Las 5S incluyen la identificación y eliminación de peligros potenciales, lo que contribuye a un entorno de trabajo más seguro en la industria automotriz.
Satisfacción del personal: Un lugar de trabajo limpio y ordenado puede mejorar la moral y la satisfacción de los empleados. Cuando los trabajadores tienen un entorno organizado y eficiente, tienden a sentirse más valorados y comprometidos con su trabajo.
Facilita la implementación de Lean Manufacturing: Las 5S son un componente clave de la filosofía Lean Manufacturing, que busca eliminar el desperdicio en los procesos de producción. Al implementar las 5S, las organizaciones de la industria automotriz están creando una base sólida para la adopción de principios Lean.
Mayor capacidad de respuesta a cambios: Un lugar de trabajo organizado es más flexible y puede adaptarse mejor a cambios en la producción o en la demanda del mercado, lo que es esencial en la industria automotriz, donde las condiciones pueden cambiar rápidamente.
Mejora la imagen de la empresa: Una organización que practica las 5S tiende a proyectar una imagen de eficiencia, calidad y profesionalismo, lo que puede ser beneficioso para su reputación en la industria y entre los clientes.
¿Cómo se aplican las 5S?
La implementación de las 5S en la industria automotriz implica un proceso bien estructurado:
Formar un equipo: Designar un equipo encargado de liderar la implementación de las 5S y formar a los empleados.
Clasificación (Seiri): Identificar y eliminar elementos innecesarios en el área de trabajo.
Orden (Seiton): Organizar y etiquetar claramente las herramientas y piezas en áreas designadas.
Limpieza (Seiso): Realizar una limpieza exhaustiva y establecer un programa de mantenimiento regular.
Normalización (Seiketsu): Establecer estándares y procedimientos para mantener las 5S en el tiempo (montar un sistema de auditorías para el control de las mismas).
Disciplina (Shitsuke): Fomentar la disciplina y la mejora continua en todo el equipo.
En este contexto, te puede interesar el post sobre cómo implantar lean manufacturing.
Ejemplos de empresas que aplican esta metodología
Varias empresas en la industria automotriz han adoptado con éxito las 5S, obteniendo resultados impresionantes en eficiencia y calidad. Ejemplos notables incluyen Toyota, Honda y Ford, que han incorporado las 5S en sus operaciones y han visto mejoras significativas en sus procesos de producción y en la satisfacción del cliente.
En conclusión, el método de las 5S emerge como una herramienta esencial en la industria automotriz, capaz de impulsar la eficiencia, calidad y seguridad en el lugar de trabajo. Al seguir las cinco etapas y aprender de las experiencias exitosas de empresas líderes, las organizaciones pueden potenciar sus operaciones y mantenerse competitivas en un mercado en constante evolución. Contacta con nosotros ante cualquier duda o conoce nuestro sistema mes para el sector automotriz.

Product Manager and Quality Systems Engineer
José Antonio Nigro
Responsable de la gestión y mantenimiento de la Norma ISO 9001:2015 y responsable de auditorías externas e internas.