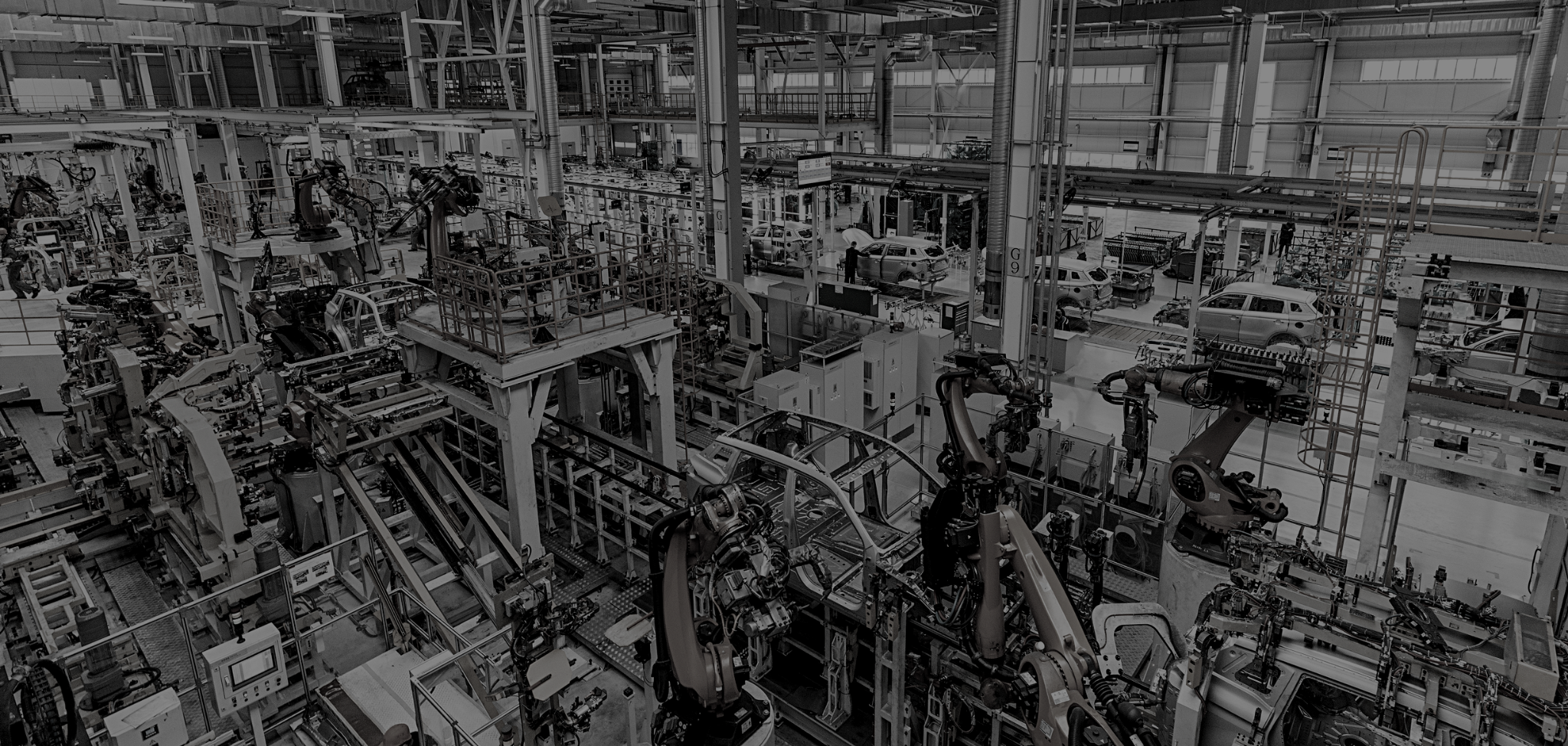
Sistema de gestión documental: Qué es y para qué sirve
Sistema de gestión documental: ¿Qué es? y ¿para qué sirve? La información es uno de los activos más importantes que tiene una empresa en la actualidad. Por ello, contar con un buen sistema de gestión documental de la producción se ha convertido en una pieza clave para garantizar la productividad de la industria 4.0. En este post te contamos qué es y sus principales beneficios. Un software de gestión documental de la producción asegura que la información industrial quede organizada de una forma segura y eficiente, de forma que las organizaciones puedan ser más rápidas en el acceso a los datos, reducir costes y garantizar la seguridad de los documentos. Para que os resulte más sencillo avanzar en el proceso de digitalización de vuestra empresa y dejéis de lado las montañas de papel y archivadores, os contamos qué es un sistema de gestión documental de la producción y para qué sirve. Antes, te invitamos a conocer el software EBR que es clave para la eliminación eficiente del papel. ¿Qué es el DMS? Un sistema de gestión documental de la producción es un software diseñado para almacenar, administrar y controlar el flujo de documentos dentro del área de producción. Este software nos permite organizar los documentos y las imágenes digitales en una localización centralizada a la que todos los miembros del equipo autorizados puedan tener acceso de forma fácil y rápida asegurando que se utilizan los documentos correctos a nivel de planta. Ahora que ya sabes qué es un sistema de gestión documental vamos a conocer sus funciones. ¿Para que sirve aplicar un sistema de gestión documental? Agilidad y seguridad serían las dos claves que resumen el cometido de este sistema. Eliminar el papel y los archivos físicos permite agilizar los procesos y sumar puntos tanto en productividad como en eficiencia energética. Además, tener todos los archivos digitalizados nos permitirá gestionar su seguridad y tenerlos bien localizados. Independientemente del origen del documento, un software de gestión documental de la producción sirve para centralizar todos los archivos de la fábrica en un mismo punto de acceso. De esta forma, un buen sistema de gestión documental permite automatizar tareas y flujos de trabajo, como la lectura de un plano o de una especificación para indexarlos a un artículo o proceso industrial con otras acciones relacionadas con la fábrica y el acceso a la información. Etapas de una gestión documental óptima Desde que un documento se crea hasta que se destruye pasa por distintas fases y todas ellas son clave para garantizar una gestión documental óptima. Para lograrlo es importante empezar por definir qué documentos forman parte de nuestros procesos, cómo podemos incluirlos en nuestro Sistema y qué información extraer y almacenar conjuntamente con los documentos en su base de datos. Una vez definida la cuestión de la información habrá que definir su ciclo de vida, cómo interactúan con los demás procesos y de qué forma podemos integrarlo en los mismos. Desgranamos el proceso en 8 pasos que os ayudarán a comprender el funcionamiento del software. Planificación. Es vital revisar y valorar la información en el contexto legal, técnico y funcional de la empresa, así como analizar las necesidades y objetivos empresariales para asentar una estrategia en materia de gestión documental. Producción. En este paso, se evalúan los documentos y su origen para categorizarlos en función de su relevancia y funcionalidad en los procesos en los que incide. Tramitación. Un sistema de gestión documental de la producción se encarga de seguir el curso del documento desde su producción hasta el cumplimiento de su función. Organización. El objetivo en esta fase es clasificar y ordenar correctamente los documentos. Transferencia. En esta fase, se definen las políticas de transferencia de los documentos, en base a su formato, migración y estructura, así como a su conservación. Disposición. El software lleva a cabo un registro sistemático que establece valores documentales, lo cual permite el seguimiento de todos los ciclos de vida de cada documento, a fin de darle su respectivo tratamiento. Mantenimiento. Uno de los principales objetivos del sistema de gestión documental de la producción es preservar la información a largo plazo. Por ello, una de las fases clave del proceso es garantizar que la documentación está correctamente protegida. Valoración. Esta fase facilita el manejo de los documentos, garantiza su selección y determina cuáles son aquellos que han perdido interés o vigencia. Cada una de estas etapas es fundamental para lograr el éxito en la gestión documental y contribuir a la mejora de las estrategias de gestión para aumentar la productividad empresarial. Beneficios frente a otros software similares Trabajar con un método de gestión documental de la producción significa digitalizar todos los documentos que antes conservábamos en papel. Con ayuda de un escáner, los documentos físicos se convierten en versiones digitales que se almacenan en una localización central. Organización: Este proceso facilita mucho la tarea de organización dentro de una institución, ya que permite ordenar la documentación y coordinar su acceso desde diferentes departamentos. Con todos los archivos digitalizados y ubicados en un mismo lugar es mucho más fácil encontrar los documentos, recuperarlos y trabajar con ellos desde cualquier sitio. Automatización: Otro aspecto importante es la automatización. Al establecer un control sobre los procesos, el software permite identificar la vigencia del documento, asegurar que el nivel correcto de ingeniería del documento es el único disponible en planta o automatizar tareas repetitivas para ahorrar tiempo y gestionar costes de la forma más óptima posible. La productividad de los procesos también aumenta gracias a tener unificada la documentación para todos los miembros del equipo y máquinas. Seguridad: Si empezamos a trabajar con un sistema de gestión documental de la producción debemos saber que este ya cumple de origen con la Ley Orgánica de Protección de Datos, el Reglamento General de Protección de Datos (RGPD) y las ISO referentes a la descripción y gestión de la documentación. Además, la gestión documental inteligente reduce el riesgo que implica trabajar con grandes volúmenes de papel y nos permite preservar a largo plazo todos los documentos