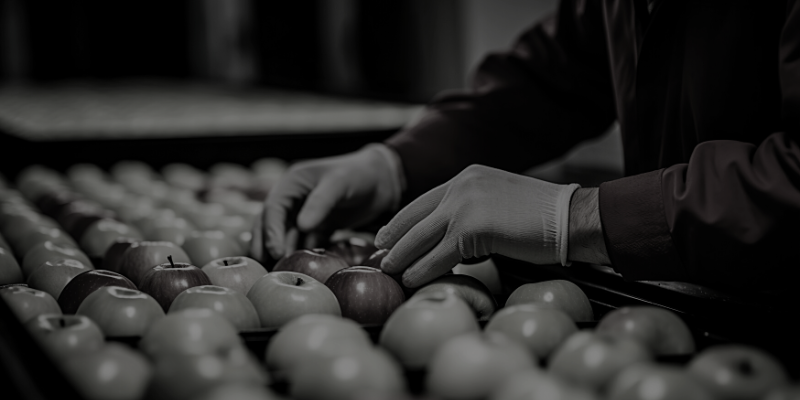
Cómo medir las desviaciones de mano de obra directa en alimentación
Cómo medir las desviaciones de mano de obra directa en alimentación En el sector de la alimentación es de vital importancia medir la desviación en el coste de mano de obra directa y analizar sus causas, para impulsar las acciones de mejora pertinentes. Se trata de uno de los principales componentes de coste en fábrica, aunque normalmente muy por debajo del coste de materia prima, especialmente en entornos productivos menos tecnificados y muy intensivos en personal. Si se permite que los costes de mano de obra se desvíen significativamente respecto a los costes estándar planificados, puede tener un impacto negativo en la rentabilidad del negocio, muy significativo en entornos con bajo margen, casi todos excepto productos “gourmet”, donde es importante hasta el segundo decimal. La medición de las desviaciones permite identificar y corregir rápidamente cualquier variación en los costes laborales y mantenerlos bajo control. Nuestro sistema MES para el sector alimentario es un gran aliado para gestionar de forma más eficiente tu fábrica por lo que te invitamos a conocerlo antes o después de leer este artículo. Índice Qué son las desviaciones de coste de mano de obra directa en una fábrica Las desviaciones en una fábrica son situaciones que se alejan de lo planeado o de lo esperado, siendo una cadena de eventos que generan un resultado negativo en la producción. Estas pueden ser causadas por errores en la gestión, maquinaria con averías o defectuosa, falta de capacitación del personal, entre otros factores. Las desviaciones en costes de mano de obra directa en una fábrica son las diferencias entre los costes reales y los costes presupuestados para los trabajadores que participan en la producción en una fábrica. Estas desviaciones pueden surgir debido a varias razones, tales como menor productividad, retrabajos, mayor participación de personal o coste/hora más alto que el coste estándar, en general, ineficiencias en la ejecución de la producción. Evaluar estas es fundamental. Medir las desviaciones de mano de obra directa en el sector alimentario Medir las desviaciones de mano de obra directa es posible al comparar el coste real de la mano de obra con el coste estándar. La complejidad se encuentra en el cálculo de ese coste real y asociarlo a un producto determinado, hay que registrar, para una determinada orden de fabricación, las personas específicas que han participado, tiempo dedicado de cada una, su coste empresa y en función de día/hora de ejecución, por citar algunos, y compararlo con el coste estándar previsto. Si el coste real es mayor que el coste estándar, se considera que existe una desviación negativa, lo que significa que los costes reales son más altos de lo que se esperaba. Por el contrario, si el coste real es menor que el coste estándar, se considera una desviación positiva, lo que indica que se gastó menos de lo planificado, y la empresa obtendrá mayores beneficios debido a la reducción de costes. Las desviaciones positivas o negativas de costes de fábrica afectan significativamente los resultados financieros de la empresa industrial, ya que equivalen al 60-80% de su facturación total, no hay partida presupuestaria más grande. Estas desviaciones, mostradas con máximo detalle, puntualmente (no el día 10 del mes siguiente) y, por supuesto, en €, hablamos de controlling de costes en tiempo real, consiguen que las empresas identifiquen y prioricen aquellas áreas donde se pueden mejorar los procesos y generar una reducción de costes más significativa, de manera recurrente además, ahorro presente que se debe mantener en el futuro. A grandes rasgos estos son los pasos que se deberían seguir para medir y actuar sobre tus desviaciones de mano de obra en fábrica: Determina el coste estándar de la mano de obra directa: implica estimar el coste que se espera en condiciones normales para producir una unidad determinada de producto o servicio. Para ello, se deben tener en cuenta factores como el salario de los trabajadores, las horas de trabajo necesarias para completar una unidad de producción y otros costes relacionados. Es importante tener en cuenta que el coste estándar de la mano de obra directa es una estimación y puede variar en función de las condiciones reales de producción. Por lo tanto, es necesario revisar y ajustar regularmente estos estándares para mantener su precisión y utilidad en la toma de decisiones. Calcula el coste real de la mano de obra directa: este coste se calcula utilizando los datos reales de la cantidad de tiempo que se ha invertido en la fabricación de un determinado producto y la tasa salarial real que se ha pagado. Calcula la desviación de coste de la mano de obra directa en €: esta desviación se extrae restando el coste estándar del coste real. Analiza la causa de la desviación: si hay una desviación significativa, es importante analizar la causa raíz de la desviación: Exceso de personal, tiempo excesivo en fabricar el producto o precio €/h superior al presupuestado. Esto se puede hacer automáticamente a través de la unión de buenas prácticas y tecnología, con alertas/mensajería para actuar en el momento o abrir proyectos que revisen el proceso productivo, la eficiencia de la mano de obra, la calidad del trabajo, la tasa salarial y otros factores que puedan afectar el coste de la mano de obra. Toma medidas correctivas: una vez identificada la causa raíz de la desviación, se pueden tomar medidas correctivas para reducir o eliminar la desviación. Esto puede incluir, mejorar los procesos, capacitar a la mano de obra, ajustar las tasas salariales y otras estrategias. Las desviaciones de mano de obra en el sector alimentario se pueden medir de diversas formas. A continuación, se presentan algunas de las medidas más comunes: Registros de producción: Los registros de producción son instrumentos importantes para medir las desviaciones de mano de obra. Estos registros pueden ser manuales en dispositivos digitales, semiautomáticos o 100% automatizados a través de geolocalización indoor. Se utilizan para comparar la cantidad de productos que se esperan producir con la cantidad real de productos producidos, en un determinado tiempo y manteniendo el equipo