La Industria 4.0 es una revolución industrial que está transformando la forma en que se fabrican los productos. Se caracteriza por el uso de tecnologías avanzadas como el internet de las cosas, sistemas ciber físicos, la inteligencia artificial y la robótica. Estas tecnologías generan una gran cantidad de datos que pueden ser utilizados por las empresas para mejorar sus procesos y productos.
La analítica de datos es esencial en la Industria 4.0 para aprovechar al máximo las tecnologías emergentes y tomar decisiones estratégicas basadas en datos con el objetivo de mejorar la eficiencia, la productividad y la competitividad de las empresas industriales.
Antes de continuar, te recomendamos leer nuestro post sobre beneficios de la inteligencia artificial en la industria.
Objetivo de la analítica de datos
El examen de datos es un proceso que permite a las empresas recopilar, almacenar, analizar y visualizar datos para identificar patrones y tendencias. Esta información puede utilizarse para tomar mejores decisiones, mejorar la eficiencia y la productividad, y crear nuevos productos y servicios.
Algunas de las características incluyen:
- Gran volumen de datos: se utiliza para analizar grandes cantidades de datos, que pueden ser demasiado grandes o complejos para ser procesados por humanos.
- Variedad de datos: además puede analizar datos de una variedad de fuentes, lo que puede ayudar a obtener una visión más completa de una situación.
- Análisis complejo: utiliza técnicas complejas para identificar patrones y tendencias en los datos.
- Visualización: usa gráficos y otras formas de visualización para comunicar los resultados del análisis a los usuarios.
El objetivo del estudio de datos es transformar los datos en conocimiento para tomar mejores decisiones, mejorar la eficiencia y la productividad, y también crear nuevos productos y servicios.
La analítica de datos puede utilizarse en varios sectores:
- Operaciones: puede utilizarse para mejorar la eficiencia de los procesos, reducir los costes e identificar áreas de mejora.
- Marketing: para segmentar a los clientes, personalizar las ofertas y recomendaciones, y medir el rendimiento de las campañas de marketing.
- Ventas: puede usarse para identificar oportunidades de venta, predecir el comportamiento de los clientes, y mejorar el servicio al cliente.
- Finanzas: para gestionar riesgos, tomar decisiones de inversión y generar oportunidades de crecimiento.
- Recursos humanos: para mejorar la gestión del talento, identificar a los mejores candidatos y desarrollar programas de formación.
El análisis de datos es una herramienta poderosa que puede ayudar a las empresas a mejorar sus resultados en una amplia gama de áreas. Las empresas que sean capaces de recopilar, analizar e interpretar datos de forma eficaz tendrán una ventaja competitiva sobre sus competidores.
Cuál es la importancia del análisis de datos en la Industria 4.0
Es mucha la importancia de la investigación de datos en la industria 4.0, pues estas tecnologías generan una gran cantidad de datos que pueden ser utilizados por las empresas para mejorar sus procesos y productos.
Debemos asegurar que los datos de partida son de calidad, fiables, bien contextualizados y están disponibles, con un buen almacenamiento y gestión del dato, para poder llegar a una buena conclusión tras su análisis. No se puede aplicar analítica avanzada con datos en papel, de ahí la importancia de la transformación digital de las empresas como punto de partida.
Es imprescindible también, tener históricos de datos correctos en gran cantidad, para poder trabajar la analítica básica y/o avanzada y entender por qué ocurren las cosas y qué pasará en función de los comportamientos de los procesos industriales.
Una herramienta MES/MOM te ayudará a cumplir estos objetivos en tu fábrica :
- Ayuda a asegurar la fiabilidad y robustez del dato, mediante la automatización de la captura de los datos adecuados en una fábrica, mediante la conexión a máquinas, sistemas, personas y productos. Conoce qué es la automatizaicón industrial exactamente en este post anterior de nuestro blog.
- Aporta contexto al dato:
- donde cuando, en que circunstancia y
- conecta con el ERP para marcar los objetivos a cumplir en la producción y conecta también con el resto de procedimientos/estándares: Calidad, Planos, Instrucciones de Trabajo, etc.
Lo almacena en una base de datos estructurada.
- A partir de esta fuente de datos valiosa de la fábrica,
- El sistema incorpora su propio motor analítico y automatiza el cálculo de, las desviaciones de Productividad y su impacto en costes de mano de obra, los costes de materia prima, cuantifica e identifica las causas de estas desviaciones e identifica las no-conformidades en Calidad en cada fabricación, para motivar acciones de mejora.
- se podrán construir modelos predictivos que se anticipen al fallo de una máquina, una no conformidad de Calidad o consigan la receta perfecta con además feed-back directo al usuario.
En el contexto de la Industria 4.0, el análisis de datos es esencial para que las empresas puedan mantenerse competitivas.
Ventajas de implementar el análisis de datos en las fábricas
La importancia de la analítica de datos en la industria 4.0 es tanta ya que existen numerosas ventajas al implementarlo:
- Mejora de la eficiencia: Muy útil para identificar áreas de mejora en los procesos de producción. Por ejemplo, puede utilizarse para identificar cuellos de botella, reducir el desperdicio y mejorar la calidad de los productos.
- Mejora de la productividad: Importante para automatizar tareas y procesos, lo que puede ayudar a las empresas a mejorar su eficiencia y productividad.
- Creación de nuevos productos y servicios: El análisis de datos puede utilizarse para identificar nuevas oportunidades de negocio. Por ejemplo, puede utilizarse para identificar nuevos productos o servicios que satisfagan las necesidades de los clientes.
- Mejora de la experiencia del cliente: Fundamental para mejorar la experiencia del cliente. Por ejemplo, puede utilizarse para personalizar las ofertas y recomendaciones, o para identificar y resolver problemas.
- Predicción de riesgos: para determinar y predecir riesgos potenciales, lo que puede ayudar a las empresas a tomar medidas para mitigarlos.
- Toma de decisiones: Para proporcionar información que ayude a las empresas a tomar mejores decisiones. Por ejemplo, puede utilizarse para identificar las mejores inversiones, los mejores clientes y los mejores productos.
- Mantenimiento predictivo: La Industria 4.0 se caracteriza por la utilización de sensores en maquinaria y equipos para recopilar datos sobre su rendimiento y estado. Con el análisis adecuado, las empresas pueden predecir fallos y distintos tipos de averías en el equipo antes de que ocurran, permitiendo un mantenimiento más proactivo y evitando costosos tiempos de inactividad.
- Mejora de la innovación: Puede utilizarse para identificar nuevas oportunidades de innovación, lo que puede ayudar a las empresas a mantenerse a la vanguardia de la competencia.
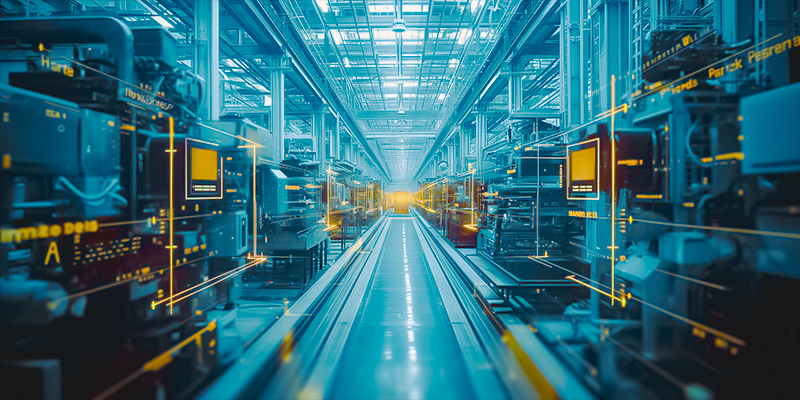
Sistema Scada
Otros fuente valiosa de datos en la fábrica, especialmente en procesos de fabricación continuos es un sistema scada.
SCADA, que significa Supervisory Control and Data Acquisition, es un sistema de control de procesos que se utiliza para supervisar y controlar dispositivos y equipos en tiempo real. SCADA recopila datos de dispositivos y equipos remotos y los envía a un centro de control central. El centro de control utiliza estos datos para monitorear el estado de los dispositivos y equipos, y para tomar medidas correctivas cuando sea necesario.
Se utiliza en una amplia gama de industrias, incluyendo la energía, el agua, el gas, la manufactura y el transporte.
La conexión a sistemas SCADA para la captura de datos e interpretación de señales de productividad, consumos o de variables de proceso puede realizarse de varias maneras.
Una forma es utilizar una interfaz de programación de aplicaciones (API) proporcionada por el proveedor del sistema SCADA. Otra forma es utilizar un software de terceros que pueda conectarse al sistema SCADA, recopilar datos y convertirlos en información, como por ejemplo un software MES.
Estos datos serán interpretados por el sistema MES, para obtener información sobre la productividad, los consumos o las variables de proceso. Esta información puede utilizarse para mejorar la eficiencia, reducir los costos, mejorar la seguridad y mejorar la calidad. De esta manera conseguiremos además conectar digitalmente toda la cadena de valor en la fábrica, desde la fabricación de un semielaborado hasta su envasado, registrando y controlando toda sus hitos de trazabilidad y resultados.
Si quieres incorporar la analítica de datos en tu empresa, te recomendamos contactar con nosotros sin compromiso. ¡Queremos llevar tu fábrica al siguiente nivel!

Adjunta a Dirección Comercial
Concepción Albert
Ingeniero Industrial con más de 15 años de experiencia en dirección y gestión de operaciones, desarrollada en el Reino Unido y España en el sector de la alimentación y otros. Acostumbrado a formar, dirigir y motivar equipos humanos orientados al logro y consecución de objetivos dentro de una cultura de Mejora Continua, así como a la creación de nuevas áreas de negocio