La industria ha avanzado a pasos agigantados en las últimas décadas con el apoyo de las tecnologías, consiguiendo así optimizar procesos y recursos, es lo que se conoce como la automatización industrial. En nuestros más de 20 años gestionando fábricas hemos sido protagonistas de esta evolución y queremos compartir sobre ella.
Este es un proceso sumamente beneficioso para las industrias que consiste en utilizar tecnologías avanzadas para controlar y operar maquinaria, sistemas y procesos en entornos de producción y manufactura.
Si quieres saber más sobre automatización industrial, en este post te contamos en qué consiste, para qué sirve, cómo puede ayudar a una industria y qué niveles existen.
Índice
Definición de automatización industrial
El término “automatización” se refiere a cualquier mecanismo que se mueve por sí mismo o que es autodeterminado. En contraposición a los sistemas manuales, los sistemas automatizados ofrecen un rendimiento superior en términos de precisión, potencia y velocidad de funcionamiento.
La automatización industrial está compuesta de una serie de procesos que buscan optimizar los recursos, minimizar errores y tiempos de inactividad, así como mejorar la seguridad en el lugar de trabajo. En ese sentido, tiene como objetivo principal aumentar la eficiencia, la productividad y la calidad en la producción, al tiempo que reduce la intervención humana en tareas repetitivas y rutinarias.
La automatización industrial implica la integración de sistemas electrónicos, mecánicos y de software para crear un entorno de producción más inteligente y autónomo lo que, sin duda, resulta muy beneficioso para cualquier industria independientemente del sector en el que opere.
Se trata entonces de un concepto fundamental en la modernización de la industria, ya que busca optimizar los procesos de producción a través de la integración de tecnologías avanzadas, con el fin de lograr una mayor eficiencia, calidad y competitividad en el mercado global.
Para qué sirve la automatización industrial
La automatización industrial ofrece numerosos beneficios, como una mayor velocidad y precisión en la producción, una reducción de los costes operativos a largo plazo, una mejora en la calidad del producto debido a una menor variabilidad y una mayor flexibilidad para adaptarse a cambios en la demanda del mercado.
Sin embargo, también puede plantear desafíos, como la necesidad de capacitación y habilidades en tecnología para los trabajadores, así como preocupaciones sobre la seguridad cibernética.
Y para superar estos retos es necesario introducir la automatización en la industria de la mano de profesionales especialista en la materia, en Mesbook, identificamos las necesidades de cada empresa para encontrar modelos productivos digitales que se adapten perfectamente a lo que cada compañía demanda.
Cómo funciona
La automatización industrial funciona mediante la implementación de tecnologías y sistemas que permiten controlar y operar procesos de producción de manera autónoma, eficiente y precisa. De forma general, la automatización industrial funciona con los siguientes elementos:
- Sensores: Los sensores son dispositivos que detectan cambios en el entorno, como temperatura, presión, nivel, velocidad, posición, entre otros. Estos sensores recopilan datos del proceso de producción y los envían a sistemas de control para su análisis.
- Sistemas de control: Estos sistemas procesan la información proveniente de los sensores y toman decisiones en función de los datos recopilados. Pueden ser controladores lógicos programables (PLCs) o sistemas de control basados en ordenadores. Los sistemas de control ejecutan programas predefinidos o algoritmos diseñados para regular y optimizar el proceso de producción.
- Actuadores: Se trata de dispositivos que toman decisiones basadas en las señales del sistema de control y realizan acciones físicas en el proceso de producción. Algunos ejemplos de actuadores incluyen motores eléctricos, válvulas solenoides, cilindros neumáticos, entre otros. Estos dispositivos controlados por el sistema de control permiten la manipulación de equipos y materiales.
- Comunicación: La automatización industrial se basa en la comunicación eficiente entre los diferentes componentes y sistemas. Los datos recopilados por los sensores se transmiten a los sistemas de control a través de redes de comunicación, como Ethernet industrial o buses de campo, lo que permite un flujo continuo de información en tiempo real.
- Programación y lógica: En la automatización industrial, se emplea la programación para definir cómo debe funcionar el proceso. Los PLCs, por ejemplo, se programan con lenguajes de programación específicos para controlar las secuencias de operación, las condiciones de activación de los actuadores y las respuestas a eventos específicos.
- Supervisión y monitoreo: La mayoría de los sistemas de automatización industrial incluyen interfaces de usuario, como pantallas táctiles o interfaces gráficas, que permiten a los operadores supervisar y controlar el proceso. Estas interfaces también proporcionan información en tiempo real sobre el estado del proceso, alarmas y datos de rendimiento.
- Retroalimentación y ajuste: La automatización industrial a menudo incorpora la retroalimentación donde los datos sobre el rendimiento y los resultados del proceso se utilizan para ajustar los parámetros y optimizar la operación. Esto puede incluir ajustes en la velocidad, la temperatura, la presión u otros factores según las condiciones cambiantes del entorno.
En MESbook, estudiamos con detalle el proceso productivo de cada uno de nuestros clientes y seleccionamos cuidadosamente los puntos de recogida de datos en las líneas y los elementos más adecuados para la obtención de estos datos de manera fiable, garantizando de este modo que toda la información esencial de la producción, se recopila de manera efectiva.
Más tarde, definimos la forma en la que dicho dato será extraído en cada uno de los sensores, actuadores y controladores de la línea realizando, por último, la instalación, programación y configuración necesarias en cada caso.
Tenemos una amplia experiencia que nos permite asegurar que la automatización de los procesos productivos alimente de manera funcional nuestro sistema y que los datos se transmitan de manera eficaz y fiable a nuestro sistema MES para reflejar la realidad de la fábrica a través de los datos provenientes de las máquinas. Esta eficiencia en la transmisión de datos proporciona información objetiva en tiempo real, sobre las pérdidas de productividad, mermas o faltas de calidad, un recurso esencial para la mejora de nuestros clientes.
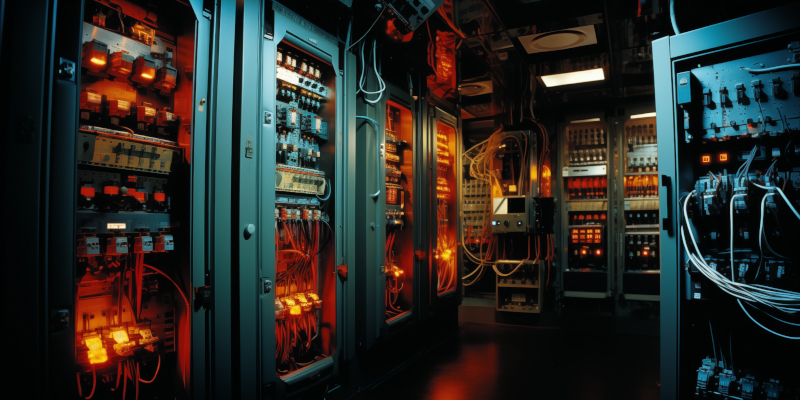
Retos de Integración de la automatización industrial
- Diversidad de Equipos y Sistemas de Control: Uno de los desafíos más destacados en la automatización industrial actual es la gestión de un parque heterogéneo de máquinas, sensores y sistemas de control en las fábricas. Esta diversidad es producto de la evolución tecnológica y la longevidad de equipos en el entorno industrial. Para asegurar una integración eficaz, se requiere una profunda comprensión de las diferentes generaciones y tecnologías, junto con la habilidad para configurar y coordinar estos dispositivos de manera que funcionen en armonía, por tanto, la experiencia en la resolución de conflictos entre sistemas dispares es fundamental para minimizar tiempos de inactividad y maximizar la eficiencia.
- Gestión de Comunicaciones Industriales y Protocolos OPC: Una de las principales necesidades de cualquier fábrica automatizada es la necesidad de comunicación eficiente entre sistemas y dispositivos, por tanto, es crucial una elección adecuada de protocolos de comunicación industrial, tales como Modbus, Comandos S7 o Profibus para intercambiar información entre CPUs y/o la configuración satisfactoria de un servidor OPC que permita recoger todos los datos disponibles en las CPUs de las máquinas. Ser capaces de acceder a la información desde diferentes tipos de dispositivos y sistemas va a depender en gran medida de la correcta implementación de estas tecnologías.
- Transformación de Datos en Conocimiento: La recopilación masiva de datos en la automatización industrial es solo el primer paso, el verdadero valor radica en la capacidad de convertir estos datos en información valiosa y conocimiento accionable. Esto implica la aplicación de algoritmos de análisis de datos para extraer patrones, identificar tendencias y tomar decisiones informadas.
- Colaboración entre Especialistas en Automatización y Gestión de fábricas: La integración exitosa de sistemas automatizados en una fábrica requiere una colaboración estrecha entre expertos en automatización industrial y profesionales de gestión de fábricas, ya que la alineación de objetivos y estrategias es esencial para lograr una operación eficiente y rentable.
- Medición de KPIs en tiempo real y Automatización Estratégica: La medición y gestión de KPIs (Key Performance Indicators) son fundamentales para evaluar y mejorar la eficiencia de la fábrica, indicadores como el OEE (Overall Equipment Effectiveness), MTBF (Mean Time Between Failures), MTTR (Mean Time To Repair) ofrecen una visión detallada del aprovechamiento de la maquinaria. Estos indicadores combinados con otros KPIS, como el coste de materiales, mermas, costes de MOD e indirectos, junto con la automatización estratégica de procesos, como el control de calidad, la logística interna con tecnologías como AGVs (Automated Guided Vehicles) y almacenes automáticos, así como la localización indoor de trabajadores, son componentes clave para avanzar hacia la Gestión Digital de la Fábrica en la era de la Industria 4.0.
Distintos niveles
La automatización de procesos industriales también se puede encontrar en diferentes clases o niveles en función del sector en el que se vayan a aplicar.
- Automatización de procesos: Se refiere a la automatización de tareas y procesos específicos dentro de una línea de producción. Esto puede incluir la manipulación de materiales, ensamblaje de productos, control de temperatura, presión y otros parámetros.
- Automatización de la gestión de la producción: Implica la integración de múltiples procesos automatizados para gestionar una línea de producción completa. Esto puede incluir la planificación de la producción, la gestión de inventarios y la coordinación de la maquinaria y los sistemas.
- Automatización de la planta: Se refiere a la automatización a nivel de toda la instalación de fabricación donde se integran diferentes líneas de producción y procesos en una sola red de control centralizada.
Los tipos de automatización industrial también pueden dividirse en fijos, programables, de automatización flexible o sistema integrado de automatización
- Automatización fija: Este tipo de automatización se utiliza para agilizar procesos específicos y, en esta, es casi imposible facilitar las modificaciones en el diseño del producto. La automatización fija es la más utilizada por el tipo de industrias que tiene que producir diseños de productos estables y sostenibles durante un largo periodo de tiempo.
- Automatización programable: Esta se utiliza generalmente para fabricar productos por lotes, el sistema de producción debe ser programado cada vez para fabricar cada lote con sus especificaciones. Este proceso de automatización requiere de tiempo cada vez que se quiere reprogramar una máquina de producción.
- Sistema de automatización flexible: Es una forma de automatización programable pero más sofisticada y refinada, ya que permite cambiar el equipo de forma automática y rápida.
- Sistema integrado de automatización: Se trata de un conjunto de máquinas, procesos y datos independientes que trabajan de forma sincrónica bajo el mando de un único sistema de control para implementar un sistema de automatización en un proceso de producción.
En la actualidad, los fabricantes se enfrentan a muchos retos en su producción fruto de encontrarse en un sistema global francamente competitivo. En ese sentido, la automatización es un gran aliado para ellos en desafíos tales como la introducción de la sostenibilidad en los sistemas de producción, enfrentarse a cadenas de suministro cada vez más complejas, el hecho de cumplir con las últimas normas de eficiencia energética o competir con empresas que cuentan con costes más reducidos por el entorno en el que operan.
Así, en Mesbook somos especialistas en industria 4.0 y aliados de las empresas que quieren llevar su línea de producción al siguiente nivel con el objetivo de convertirse en compañías más eficientes y competitivas. Consúltanos y estudiaremos tu industria para crear un plan de maestro de transformación digital que se adapte a tus necesidades. Contacta con nosotros.

Ingeniero de automatización en MESbook
Antonio Motos Carvajal
Ingeniero electrónico con 2 años de experiencia en automatización industria