¿Es sencilla la detección de motivos de pérdida de OEE? Hay muchas formas de hacerlo y todas son válidas pero deben estar reguladas y correctamente registradas. Además, es importante contar con un análisis correcto para conocer y detectar las pérdidas.
El OEE (Overall Equipment Effectiveness) es una métrica que mide la eficacia global de los equipos en la producción. Se utiliza para medir la producción y los costes, y para identificar oportunidades de mejora en los procesos de producción. Como puedes ver en nuestro post de cómo se calcula el OEE se hace multiplicando la disponibilidad, la eficiencia del equipo y la calidad del producto. El objetivo es maximizar la eficiencia y minimizar el tiempo de inactividad.
En resumen, el OEE mide cuánto produce el equipo en comparación con su capacidad máxima para producir un determinado artículo. Una disminución en el OEE implica una pérdida de la eficacia del equipo, lo que puede ser causado por varios motivos:
- Microparadas y averías: Son imprevistos que detienen la producción y requieren reparaciones.
- Tiempos de inactividad planificados: Detenciones programadas para mantenimiento o paros programados para descansos.
- Cambios de productos: El tiempo de cambio entre un producto y otro puede ser prolongado y ocasionar retrasos en la producción.
- Pérdidas de velocidad: El equipo funciona por debajo de su capacidad máxima o con una velocidad más lenta que la requerida para una producción efectiva.
- Defectos de calidad: Productos que no cumplen con los estándares de calidad establecidos.
Factores que afectan al OEE
Como ya sabes, el OEE, es un indicador que mide la eficiencia de un equipo o una planta de producción en términos porcentuales de la producción total que se debería estar produciendo en el mismo tiempo.
Para lograr una alta eficiencia del equipo, es necesario que se consideren muchos factores que pueden afectar el rendimiento y ocasionar pérdidas. Por esto, es importante la correcta detección de motivos de pérdida de OEE.
Uno de los principales factores que afectan al OEE es el tiempo de inactividad del equipo, es decir, el tiempo en el que la maquinaria no está produciendo o está parada. Estos tiempos de inactividad pueden ser causados por diversas razones, como fallos en la maquinaria, mantenimiento programado, esperas por materiales o falta de personal, entre otros.
Otro factor que puede afectar a la eficiencia del equipo es el tiempo de ciclo de producción, es decir, el tiempo que tarda el equipo en fabricar el producto completo. Un ciclo de producción prolongado significa que el equipo está produciendo menos unidades que las esperadas por turno, lo que contribuye a disminuir el OEE.
Asimismo, la tasa de calidad es un factor clave que afecta al OEE. Cuando se producen defectos en los productos, ya sea por errores de la maquinaria o por errores humanos, eso implica que se están produciendo menos unidades de calidad, y por lo tanto, la eficiencia disminuye. Y lo que es peor, se han dedicado recursos industriales, humanos, energéticos y materiales a fabricar producto defectuoso que en ocasiones es completamente inservible y en otros requiere de un sobrecoste para reprocesarlos.
Por último, el rendimiento podría verse afectado por la falta de formación y capacitación de los operarios, así como por la falta de herramientas, maquinaria y tecnología adecuadas.
En definitiva, hay algunos factores principales, además de los mencionados anteriormente, que inciden en la eficiencia del equipo, y es importante analizarlos uno por uno para la detección de motivos de pérdida de OEE. De esta manera, podrán tomarse las medidas adecuadas para corregirlos y mejorar.
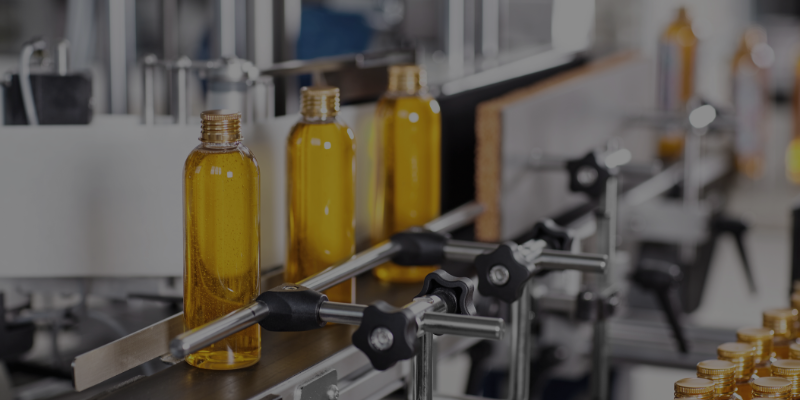
Principales pérdidas en una fábrica
El OEE como herramienta se utiliza para determinar las pérdidas o fugas en el proceso de producción, lo que ayuda a identificar áreas de mejora y aumentar la eficiencia en la producción. Se considera que existen tres tipos principales de pérdidas en una fábrica:
- Pérdidas por disponibilidad: se refiere a las interrupciones del proceso de producción debido a averías, fallas en el equipo o cambios de herramientas. Esto afecta la disponibilidad de la maquinaria y reduce la eficiencia en la producción.
- Pérdidas por rendimiento: esto se debe a las ineficiencias en el proceso de producción, como problemas con la velocidad de producción o en la calidad de los productos. También puede estar relacionado con problemas en el ajuste de los equipos o el rendimiento de los operadores.
- Pérdidas por calidad: esto se refiere a las pérdidas asociadas con productos que no cumplen con los estándares de calidad. Esto puede deberse a problemas de materiales, problemas con el equipo de producción o errores humanos en el proceso de fabricación.
En general, el objetivo de medir el OEE es reducir estas tres pérdidas en una fábrica. Con la identificación de estas áreas de mejora, las empresas pueden implementar estrategias y prácticas de producción más eficientes para maximizar la producción y minimizar las pérdidas. Al mejorar la eficiencia de la producción, las empresas pueden aumentar su rentabilidad y mejorar su competitividad en el mercado.
Cómo detectar los motivos de pérdida de OEE
El Índice de Eficacia Equipo es una herramienta importante para medir el rendimiento global de un equipo de producción. Así puede funcionar el rastreo de motivos pérdidas de OEE:
- Analizar los datos: Recopilar todos los datos relevantes sobre el rendimiento y la eficiencia del equipo de producción. Analizar estos datos te ayudará a identificar el tipo de pérdidas que están ocurriendo.
- Identificar las pérdidas: Analizar y clasificar las pérdidas en las tres categorías: pérdidas por tiempo de inactividad, pérdidas por velocidad y pérdidas por calidad. Esto te ayudará a identificar el tipo de pérdida en el rendimiento del equipo.
- Identificar los motivos: Una vez que hayas identificado los tipos de pérdidas, debes profundizar en cada una e identificar las causas-raíz. Por ejemplo, si las pérdidas por tiempo de inactividad se deben a problemas mecánicos, debes identificar las piezas que causan problemas y trabajar en mejorarlas.
- Asignar prioridades: Después de identificar los motivos de pérdida y causas raíz, es importante asignar prioridades. Esto te permitirá trabajar en las causas más importantes primero, lo que te permitirá una mejora rápida y significativa en el rendimiento del equipo.
- Tomar medidas: Finalmente, debes tomar medidas para abordar los motivos de pérdida identificados. Asegúrate de que estas medidas sean efectivas y que se ajusten a las prioridades asignadas.
Como conclusión: la detección de los motivos de pérdida de OEE se realiza mediante la recopilación de datos, la identificación de las pérdidas, la identificación de los motivos de pérdida, la asignación de prioridades y la toma de medidas efectivas. Este proceso es crucial para mejorar la eficiencia y el rendimiento de la línea de producción.

Adjunto a Dirección Comercial en MESbook
Arturo Torres
Ingeniero industrial con más de 27 años de experiencia en distintos sectores como director de operaciones, Supply Chain, Procesos y Calidad. Docente en instituciones como la Cámara de Comercio y el Consejo General de la Ingeniería Técnica Industrial de España.