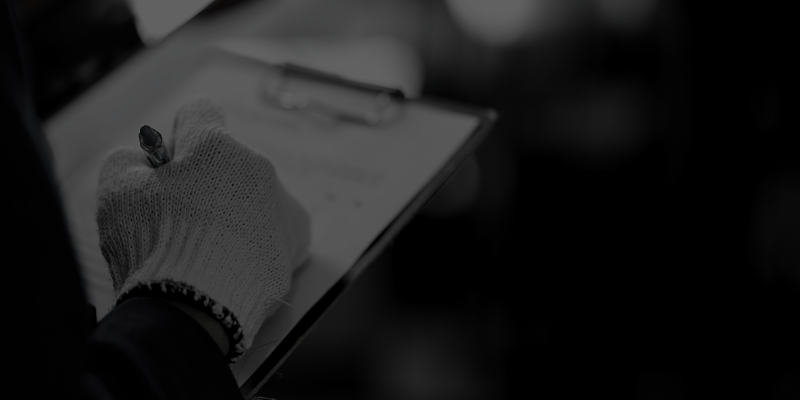
Control de incidencias: qué es y consejos
Control de incidencias: qué es y consejos La industria manufacturera es un sector altamente complejo y dinámico que puede conllevar a una gran cantidad de problemas en los procesos productivos y operativos. Por esta razón, tener un buen sistema de control de incidencias es fundamental para cualquier fábrica. El control de incidencias permite a las fábricas identificar y gestionar cualquier problema o fallo que pueda surgir en los procesos productivos y puede ayudar a reducir tiempos muertos y a solucionar problemas de manera más rápida y efectiva, lo que a su vez puede mejorar la eficiencia de la producción y reducir los costes de producción. Además, un buen sistema de control de incidencias puede ayudar a mejorar la calidad de los productos. Por último, este también puede ser importante para la seguridad en la fábrica. Además, el análisis de incidencias puede ayudar a identificar patrones y tendencias, lo que permite a la fábrica tomar medidas proactivas para prevenir futuros problemas de seguridad. Índice Qué es el control de incidencias Un sistema de control de incidencias es una herramienta informática, generalmente un software, que se utiliza para prevenir, gestionar y registrar las incidencias o problemas que puedan surgir en un servicio o sistema. Este sistema permite a los usuarios informar de las incidencias que han detectado, y a los encargados del mantenimiento y solución de problemas para realizar un seguimiento y solucionar las incidencias de forma más rápida y eficiente. El sistema de control de incidencias permite registrar la información necesaria para solucionar el problema, como la descripción de la incidencia, fecha y hora en que se detectó, usuarios afectados, etc. Además, proporciona un registro histórico de las incidencias ocurridas y las soluciones aplicadas, lo que puede ser útil para mejorar el servicio en el futuro. Algunas de sus ventajas son: Mayor eficiencia: el control de incidencias permite a los encargados de la fábrica responder rápidamente a cualquier problema o incidencia que surja. Mayor precisión: con un software de control de incidencias, es posible registrar y realizar un seguimiento detallado de todas las incidencias en la fábrica, lo que implica una mayor precisión a la hora de identificar y solucionar los problemas. Gestión de recursos: gracias a la información proporcionada por un software de control de incidencias, los encargados de la fábrica pueden tomar decisiones más adecuadas. Control de costes: permite identificar áreas de mejora y reducir costes asociados a la producción. Mejora de la calidad: un software de control de incidencias permite a las empresas identificar problemas de no calidad en la producción y solucionarlos de forma rápida antes de que la incidencia se convierta en una no conformidad. Consejos para una gestión de incidencias efectiva Estos son algunos de los principales consejos para una correcta gestión de un software de control de incidencias: Establecer un sistema de seguimiento y control: Es fundamental contar con un sistema que permita detectar y registrar las incidencias que surjan en la fábrica. Este sistema debe ser fácil de usar y mantener. Asignar responsabilidades: Es importante establecer las responsabilidades de los diferentes departamentos o unidades de la fábrica en relación con las incidencias. Debe haber una persona encargada de la gestión de incidencias y coordinarse con los departamentos pertinentes para la solución de las mismas. Identificar y priorizar las incidencias: Es necesario identificar las incidencias que pueden provocar mayores impactos en el proceso productivo y priorizarlas para su solución inmediata. Establecer protocolos de actuación: Es conveniente contar con protocolos de actuación predefinidos para los diferentes tipos de incidencias que puedan surgir. Esto permite actuar de forma rápida y eficiente ante un problema. Comunicación efectiva: Es fundamental contar con una buena comunicación entre los diferentes departamentos y personas implicadas en la gestión de incidencias. Se debe contar con un canal de comunicación claramente establecido para informar sobre las incidencias detectadas y para coordinar la solución de las mismas. Formación y sensibilización: Todos los empleados de la fábrica deben ser formados y sensibilizados sobre la importancia de la gestión de incidencias y su implicación en el proceso. La prevención es siempre mejor que la solución de problemas. Análisis de causas: Es importante realizar un análisis de las causas de las incidencias para identificar las causas raíz. De esta manera, se pueden establecer medidas preventivas para evitar su repetición en el futuro. Evaluación y mejora continua: Es fundamental evaluar el desempeño del sistema de gestión de incidencias y establecer planes de mejora continua para corregir las desviaciones detectadas y mejorar la eficacia del sistema. Si te interesa la gestión y control de incidencias en una fábrica, te recomendamos también leer nuestro post sobre tipos de averías de maquinaria industrial y cómo controlarlas dado que este es un punto clave en producción que no siempre se monitoriza adecuadamente. Cómo comunicarlas Para comunicar las incidencias de una fábrica se deben seguir los siguientes pasos: Seleccionar un software adecuado: existen diversos programas informáticos que permiten la gestión de incidencias y no conformidades en una fábrica. Es importante elegir un software que se adapte a las necesidades de la empresa. En MESbook contamos con Leanbook, un sistema basado en la metodología Lean que ofrece conexión entre los problemas que se identifican en las fábricas y sus soluciones. Todo ocurre en tiempo real y conecta máquinas con procesos, sistemas, etc. Registrar la incidencia: cuando se identifica un problema, se debe registra en el software o el propio software debe hacerlo. Es importante incluir toda la información relevante, como la descripción del problema, su grado de urgencia… Asignar la incidencia: se debe asignar a un técnico o responsable para que la resuelva. Realizar el seguimiento de la incidencia: mientras se soluciona la incidencia, se debe realizar un seguimiento periódico del estado del problema. Esto permite determinar si la solución está progresando adecuadamente o no. Dar solución a la incidencia: cuando se ha solucionado el problema, se debe actualizar el registro del software. Si la solución fue efectiva, se puede cerrar la incidencia. Generar informes: sobre la frecuencia y la naturaleza de los problemas. Estos informes pueden