¿Te interesa saber cómo mejorar la productividad industrial? Hay diferentes métodos y técnicas más y menos exitosas para conseguirlo. En Mesbook somos expertos en sistemas de gestión de la producción en empresas industriales y queremos ayudarte.
Lo primero que necesitas llevar a cabo es un buen análisis y una medición correcta. Si no mides no controlas, y si no controlas no conoces todo tú margen de mejora, ni tampoco podrás conocer la eficacia de las nuevas acciones de mejora para una empresa industrial.
¿Qué es la mejora de la productividad industrial exactamente?
Pero antes de conocer los métodos y técnicas de productividad, debes tener claro qué significa mejorar la productividad industrial y redefinir algunas ideas de mejora en producción. Además, por supuesto, de conocer cuál es la productividad de tu fábrica y saber calcularla mediante la métrica OEE.
La mejora de la productividad industrial consiste en aumentar los ingresos, beneficios, competitividad, posición en el mercado, niveles de producción, etcétera, en base a un estudio de trabajo pormenorizado y eficiente, y al análisis del proceso productivo de la empresa. Para esto se tienen en cuenta la ingeniería de métodos y los estudios de tiempos, entre otras soluciones.
Y como mejorar la productividad de una fábrica o empresa no es sencillo, esta ingeniería de métodos y estudios de tiempo se desgranan y subdividen en técnicas de fácil aplicación y medición.
¿Estás preparado para conocerlas? Vamos a ello, pero antes te puede interesar este artículo sobre cómo reducir costes en una empresa industrial.
Técnicas para mejorar la productividad industrial:
El estudio del trabajo tiene un papel fundamental en la productividad de cualquier empresa y consiste en una evaluación sistemática de todas las actividades. El estudio de trabajo está dividido en la ingeniería de métodos y los estudios de tiempo, como ya has leído antes.
- La ingeniería de métodos es el registro y análisis de las diferentes formas de ejecución de las actividades. Su objetivo es encontrar mejoras para diseñar una nueva forma de realizar esas mismas actividades, pero de una forma más rápida y sencilla, mejorando el control de calidad.
- Los estudios de tiempo son un conjunto de técnicas que se emplean para averiguar el tiempo que invierte un trabajador estándar en una determinada tarea preestablecida. El fin por supuesto, es mejorar la cifra sin que repercuta a la calidad.
En base a estos dos conceptos, aparecen 8 etapas imprescindibles que permiten saber cómo mejorar la productividad industrial en cada caso particular. Porque la respuesta a la pregunta no es exacta, ya que cada negocio, sector, industria, empresa… está sometida a un sinfín de variables. Eso sí, ahorrar costes en automoción o en otros sectores es más sencillo aplicando los sistemas adecuados.
Estas 8 etapas son: seleccionar, registrar, examinar, establecer, evaluar, definir, implantar y controlar. Y todos los procesos y actividades de la industria deberán pasar por ellas.
Métodos de productividad a aplicar
Y de ellas surgen los métodos de productividad que se encuentran en cualquier propuesta de mejora de una empresa:
- Líneas de producción automatizadas: Si quieres saber cómo mejorar la productividad industrial, no dudes en que aún quedan tareas y actividades por automatizar. Para ello necesitas conocer el funcionamiento de cada una de ellas y sin duda encontrarás espacios que podrán ser automatizados y con ellos mejorar la productividad alejando el error humano.
- Maquinaria óptima: para cualquier tarea en el sector industrial se precisa una maquinaria adecuada. En un primer momento puede resultar un alto ingreso, pero en poco tiempo se rentabiliza, porque mejora los tiempos de producción, la calidad, reduce errores y permite incorporar cambios o nuevas líneas de producción.
- Monitorización sistemática: otro método para mejorar la productividad de una empresa es la monitorización. Este método se encuentra en las etapas de registrar y examinar, pero las empresas lo abandonan tras recabar una serie de datos. El método adecuado es convertirlo en sistemática y continua.
- Detectar puntos clave: es esencial tener un método para detectar los puntos de máxima productividad y los de menor rendimiento o más fallos. Será la única forma de conocer las fortalezas y debilidades y aumentarlas y eliminarlas, respectivamente.
- Tareas sin intervención humana: Al igual que existe un número mayor de tareas que pueden automatizarse, también existe un gran número de tareas en los que la intervención humana no está siendo de ayuda. La compra de maquinaria que lo sustituya puede parecer arriesgada o incluso puede representar una inversión mayor. Pero con miras en el medio y largo plazo, será un beneficio.
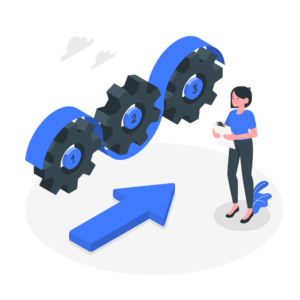
Errores más frecuentes
Ya sabes cómo mejorar la productividad de una empresa con 5 métodos diferentes, pero aplicarlos no implica que tu compañía no pueda caer en algunos de los errores más frecuentes. Para evitarlos, las 8 etapas deben estar siempre presentes en los diferentes métodos o técnicas.
Algunos de los errores más frecuentes a la hora de aplicar las técnicas de mejora de la productividad son: las mediciones incorrectas o incompletas, la maquinaria de última tecnología que no está diseñada para la tarea que se le encomienda, la automatización en tareas que necesitan supervisión o procesos de análisis más complejos y otras como la ausencia de personal cualificado o la falta de feedback entre procesos.
Casos de éxito en la mejora del rendimiento en fábricas
Existen muchos ejemplos ilustrativos y casos de éxito que permiten conocer al avance y cambio que supone la implementación de las técnicas de mejora de la productividad.
Uno de los casos es Lamborghini. La conocida marca de coches deportivos de lujo necesitaba tener un control más preciso de los tiempos y gestionar mejor tanto la producción como el mantenimiento. Y cuando aplicó algunos de los métodos y sometió cada uno a las 8 etapas, mejoró en las 4 áreas funcionales: producción, material, calidad y mantenimiento.
Por otro lado, Toyota sabe cómo mejorar la productividad industrial pues ha sido y sigue siendo un caso de éxito en todos los aspectos. Tanto, que parte de sus altos cargos actúan como guías de otras empresas de variada índole como perfumerías, farmacéuticas… Toyota creó el método Kanban (Kanban de pedido y Kanban de producción) y los flujos pull que son técnicas básicas para incrementar la productividad.
- El Kanban de pedido ayuda en la comunicación entre procesos.
- El Kanban de producción sirve para reorganizar la producción, fabricar nuevos ítems y reemplazar.
El método Kanban de Toyota tiene muchas ventajas, por ejemplo, reduce el papeleo al mínimo, consigue empleados más responsables, asegura el stock necesario, permite un mejor control de la producción, etcétera. Sin duda, implementar un sistema de trazabilidad empresarial efectivo es una de las claves.
En Mesbook tenemos el objetivo de alcanzar un sistema de gestión de fábricas eficiente y en tiempo real para todos nuestros clientes. Contacta con nosotros sin compromiso y descúbre todas las soluciones que podemos aportar a tu negocio.