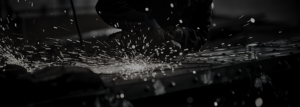
¿Qué es la Industria 4.0?: todas las claves
¿Qué es la Industria 4.0?: todas las claves Mucho se habla de la transformación digital de las empresas industriales y de sus múltiples ventajas . Pero, ¿realmente sabemos qué es la Industria 4.0? Desde MESbook vamos a explicar con todo detalle las incógnitas alrededor de este proceso de digitalización para que entiendas de primera mano qué puede aportarle a tu empresa. Te invitamos a seguir leyendo pero puede que antes te interese conocer algunas aplicaciones de la industria 4.0. Definición de Industria