La industria del automóvil es una de las más importantes del mundo y se caracteriza por la alta competitividad y la exigencia de los clientes en cuanto a la calidad y seguridad de los productos. Por lo tanto, el aseguramiento de la calidad es un factor crucial en la industria del automóvil y se refiere a todas las medidas adoptadas para garantizar que los productos cumplen con los estándares de calidad y seguridad requeridos por los clientes y la legislación.
En la industria automotriz el aseguramiento de la calidad se enfoca en garantizar que los vehículos se diseñen, fabriquen y entreguen con los más altos estándares de calidad, fiabilidad y seguridad.
Aspectos clave del aseguramiento de la calidad en la industria del automóvil
Diseño de producto: El aseguramiento de la calidad comienza desde la etapa de diseño del producto, donde los fabricantes de automóviles tienen que asegurarse de que los vehículos se diseñen con los estándares de calidad y seguridad necesarios. Esto implica realizar pruebas rigurosas en los prototipos y modelos conceptuales para identificar y solucionar problemas de calidad antes de que los vehículos se fabriquen en serie.
Procesos de fabricación: Los fabricantes de automóviles también deben asegurarse de que los procesos de fabricación sean consistentes y confiables. Esto implica la implementación de controles de calidad en cada paso del proceso de producción, desde la adquisición de materiales hasta el ensamblaje final del vehículo. También se realizan pruebas en línea durante la producción para identificar problemas de calidad y solucionarlos de inmediato.
Inspección de calidad: La inspección de calidad es otra parte importante del aseguramiento de la calidad en la industria del automóvil. Se realizan pruebas en los vehículos terminados para identificar cualquier problema de calidad, como defectos de fabricación o problemas de rendimiento. Esto se hace mediante pruebas rigurosas, como pruebas de choque, pruebas de durabilidad y pruebas de rendimiento en carretera.
Garantía de calidad: Los fabricantes de automóviles también ofrecen garantías de calidad para asegurarse de que los clientes estén satisfechos con sus productos. Esto incluye garantías de rendimiento y durabilidad, así como garantías de satisfacción del cliente. Las garantías son una forma de asegurar que los clientes estén satisfechos con sus vehículos y que los fabricantes de automóviles mantengan su reputación de calidad y seguridad.
Metodologías para el aseguramiento de la calidad en el sector automoción
De entre las muchas metodologías que existen, en este sector se han consolidado dos:
- Six Sigma
- Lean Manufacturing
Lean Manufacturing y Six Sigma son dos metodologías empresariales diferentes pero complementarias que se utilizan para mejorar la eficiencia y la calidad de los procesos de producción.
1. Six Sigma
Six Sigma, por otro lado, se enfoca en la eliminación de la variación en los procesos de producción. Se basa en la idea de que la calidad de un producto o servicio puede medirse a través de la variación en los procesos de producción, y busca reducir esta variación para mejorar la calidad. Los principios fundamentales de Six Sigma incluyen la definición clara del problema, la medición precisa de la variación, el análisis detallado de los datos, la mejora continua y la estandarización.
Ambas metodologías comparten el objetivo de mejorar la eficiencia y la calidad de los procesos de producción. Lean se enfoca en la eliminación de desperdicios y Six Sigma se enfoca en la eliminación de la variación. Al combinar ambos enfoques, las empresas pueden mejorar la calidad de sus productos y servicios, reducir costos y aumentar la satisfacción del cliente.
La integración de Lean y Six Sigma se conoce como Lean Six Sigma, y es una metodología muy efectiva que combina lo mejor de ambos enfoques. Con Lean Six Sigma, las empresas pueden mejorar los procesos de producción de manera más completa y sostenible, y lograr mejores resultados a largo plazo.
El enfoque de Six Sigma es una metodología utilizada para mejorar la calidad de los procesos y productos en la industria del automóvil. Six Sigma se basa en una filosofía de reducción de variabilidad y mejora continua.
En el enfoque de Six Sigma, se utiliza un enfoque sistemático y basado en datos para identificar y eliminar las causas de la variabilidad en los procesos. La metodología se centra en la eliminación de defectos y la reducción de la variabilidad para mejorar la calidad de la industria automotriz y reducir los costos.
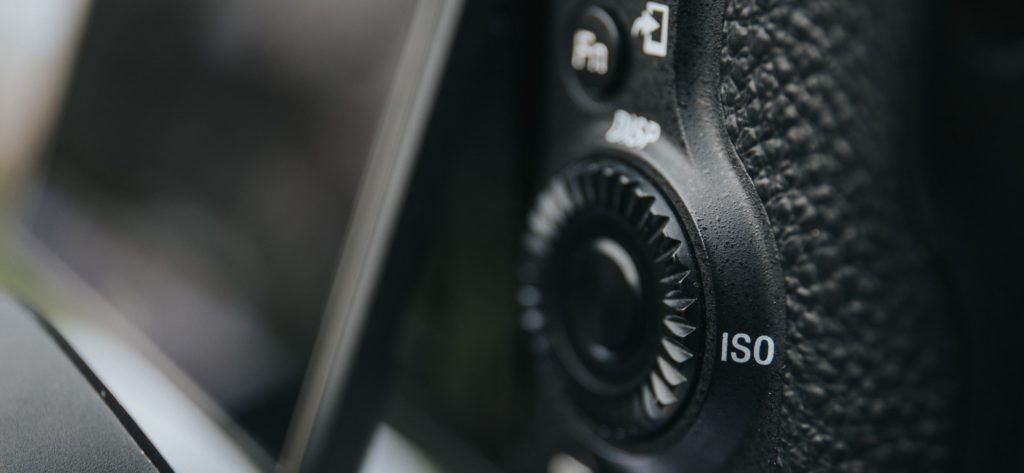
DMAIC: El enfoque de los 5 pasos de Six Sigma
Six Sigma utiliza un enfoque de cinco pasos conocido como DMAIC (Definir, Medir, Analizar, Mejorar y Controlar). A continuación, se describen brevemente cada uno de los pasos de DMAIC:
- Definir: Se define el problema y se establecen los objetivos del proyecto. También se identifican los clientes y se determinan sus requisitos.
- Medir: Se recopilan datos sobre el proceso y se realiza un análisis de la capacidad del proceso. Se utilizan herramientas como el gráfico de control y la hoja de verificación para recopilar y analizar los datos.
- Analizar: Se analizan los datos recopilados en la etapa de medición para identificar las causas de la variabilidad en el proceso. Se utilizan herramientas como el análisis de causa raíz y el diagrama de Ishikawa para identificar las causas fundamentales de los problemas.
- Mejorar: Se implementan soluciones para abordar las causas identificadas de la variabilidad en el proceso. Se utilizan herramientas como el diseño de experimentos para identificar la mejor solución y se implementa un plan de mejora.
- Controlar: Se establece un sistema de control para monitorear el proceso y garantizar que se mantenga dentro de los límites establecidos. Se utilizan herramientas como el gráfico de control para monitorear el proceso y se implementa un plan de control.
Six Sigma: Metodología para mejorar la calidad y reducir costes
El enfoque de Six Sigma es una metodología importante utilizada en la industria del automóvil para mejorar la calidad y reducir los costos. Se utiliza para mejorar los procesos de producción, reducir los defectos en los productos y mejorar la satisfacción del cliente. Los beneficios del enfoque de Six Sigma incluyen una mayor eficiencia en el proceso, reducción de los costos de producción y mejora de la satisfacción del cliente. Cabe destacar que se basa en un enfoque sistemático y basado en datos para identificar y eliminar las causas de la variabilidad en los procesos. También se utiliza en combinación con otras herramientas y metodologías, como APQP y la Casa de la Calidad, para garantizar la calidad del producto en la industria del automóvil.
En resumen, el aseguramiento de la calidad es un factor clave en la industria del automóvil y abarca todos los aspectos de la producción de vehículos, desde el diseño hasta la entrega al cliente. Los fabricantes de automóviles tienen que implementar medidas rigurosas de aseguramiento de la calidad para garantizar que sus productos sean seguros, confiables y satisfagan las expectativas de los clientes.
De esta manera, pueden mantener su posición competitiva en el mercado y asegurarse de que sus productos sean bien recibidos por los clientes.
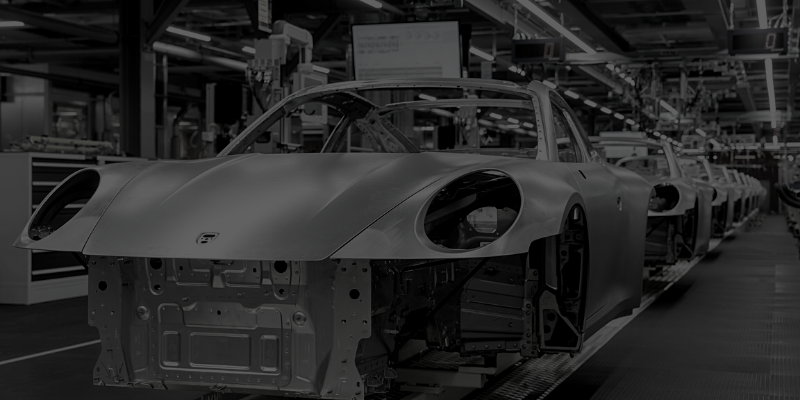
2. Lean Manufacturing
Por otro lado, Lean Manufacturing es una metodología de gestión empresarial que se enfoca en la eliminación de desperdicios y actividades innecesarias en los procesos de producción, con el objetivo de mejorar la eficiencia y reducir los costos. La metodología se originó en Toyota durante la década de 1950 y desde entonces se ha convertido en un enfoque popular para la mejora continua en la producción y los procesos empresariales.
El término «lean» significa «magro» en inglés y se refiere a la idea de reducir el exceso de grasa o desperdicio en los procesos empresariales. La filosofía central de Lean Manufacturing es agregar valor al producto o servicio eliminando todas las actividades que no agregan valor al mismo.
Principios fundamentales de la metodología Lean Manufacturing
La metodología de Lean Manufacturing se basa en cinco principios fundamentales:
- Valor: se refiere a lo que el cliente está dispuesto a pagar por el producto o servicio. El objetivo es comprender lo que el cliente necesita y enfocar los procesos empresariales para satisfacer esas necesidades.
- Flujo de valor: se refiere a la secuencia de actividades que se necesitan para crear el producto o servicio. El objetivo es eliminar todas las actividades que no agregan valor y reducir el tiempo que tarda el producto en moverse a través del proceso de producción.
- Flujo de trabajo continuo: se refiere a la eliminación de las interrupciones y los cuellos de botella en el proceso de producción. El objetivo es mantener el flujo de trabajo constante y continuo.
- Producción justa a tiempo: se refiere a la entrega del producto o servicio en el momento justo en que el cliente lo necesita. El objetivo es evitar la sobreproducción y reducir los inventarios.
- Mejora continua: se refiere a la búsqueda constante de formas de mejorar los procesos empresariales. El objetivo es lograr una mejora continua en la calidad, la eficiencia y la satisfacción del cliente.
La metodología de Lean Manufacturing utiliza herramientas y técnicas específicas para identificar y eliminar los desperdicios en los procesos empresariales. Algunas de estas herramientas incluyen el mapeo de flujo de valor, el análisis de las 5S, el Kanban, el Poka-Yoke y el Kaizen.
En resumen, Lean Manufacturing es una metodología de gestión empresarial que se enfoca en la eliminación de desperdicios y actividades innecesarias en los procesos de producción, con el objetivo de mejorar la eficiencia y reducir los costos. Al seguir los principios fundamentales de Lean, las empresas pueden mejorar la calidad de sus productos y servicios, reducir los tiempos de entrega y aumentar la satisfacción del cliente.
En MESbook entendemos que la combinación de ambas soportadas por la tecnología digital que facilite su implantación y sostenibilidad es fundamental para dar un paso adelante en la competitividad y búsqueda de la excelencia industrial. Por eso MESbook ha desarrollado estas tecnologías para guiar y ayudar a las empresas en esta búsqueda de la excelencia.
Si quieres saber más, contacta con nosotros.

Customer Success Management Director
Arturo Torres
Ingeniero industrial con más de 27 años de experiencia en distintos sectores como director de operaciones, Supply Chain, Procesos y Calidad. Docente en instituciones como la Cámara de Comercio y el Consejo General de la Ingeniería Técnica Industrial de España.