Una gestión inteligente de la producción es clave para mejorar la productividad de una fábrica. Como toda revolución, la digitalización requiere de una evaluación previa y, para ello, tenemos la fórmula. Saber cómo calcular el OEE de una fábrica nos guiará a la hora de introducir las mejoras necesarias para mejorar nuestro rendimiento productivo.
Puedes conocer en profundidad la definición de OEE en este post que enlazamos, pero se trata de herramienta estratégica para monitorizar la capacidad productiva de la maquinaria y optimizar el empleo de recursos materiales y financieros. Te explicamos en qué consiste este cálculo y cómo aplicarlo para adecuar tu producción a la Industria 4.0.
¡Sigue leyendo!
Pasos para calcular el OEE de una fábrica
El cálculo del OEE (Eficacia Global de los Equipos) nos indica cómo medir la eficiencia en una planta de producción y es una fórmula necesaria si queremos apostar por la mejora continua y conseguir casos de éxito con nuestra empresa.
El objetivo de esta métrica es sencillo, su cálculo nos permite comparar el rendimiento actual de la maquinaria con su capacidad máxima de producción:
- Si el OEE es bajo, significa que hay margen de mejora y que, por tanto, necesitamos introducir nuevos sistemas para aumentar la productividad de nuestros procesos.
- Por el contrario, si el cálculo se acerca al 100% nos indica que nos aproximamos a la máxima capacidad de producción.
Para calcular el OEE de una fábrica hemos de desgranar y comprender los tres conceptos que componen la fórmula.
OEE = Disponibilidad * Rendimiento * Calidad.
La disponibilidad de la máquina se calcula en función del tiempo de funcionamiento y de las horas de trabajo programadas. Cuanto más tiempo se produzca, mayor será la disponibilidad, mientras que cuanto más baja sea la cifra de disponibilidad no estará diciendo que más tiempo ha estado parada la maquinaria.
Disponibilidad % = (Tiempo en producción / Tiempo programado para producir) * 100 %
- La calidad es el índice utilizado para medir los productos y las piezas defectuosas que no pueden ser entregadas al cliente. Supervisar constantemente la producción en serie nos ayudará a optimizar el empleo de recursos.
Calidad % = (Cantidad de productos buenos / Cantidad total producida) * 100 %
- El rendimiento evalúa el ritmo de producción y compara la velocidad de producción de un determinado artículo con la cantidad teórica que podría haberse producido durante el tiempo que la maquinaria ha estado en funcionamiento.
Rendimiento % = (Cantidad de producción real / Cantidad de producción teórica) * 100%
En definitiva, un resultado positivo se traduciría en que sólo se fabrican piezas de calidad lo más rápido posible y sin tiempo de parada.
¿Por qué utilizar este indicador para medir la productividad de tu empresa?
Medir los resultados es imprescindible si aspiramos a mejorar la eficiencia de los procesos productivos de nuestra fábrica e introducir sistemas de mejora. Esta es la función del OEE, sin esta fórmula estaríamos avanzando hacia la industria 4.0 con los ojos vendados.
Implementar correctamente un sistema OEE repercute directamente en el rendimiento y la productividad de los procesos industriales. Su cálculo nos permite reducir los tiempos en los que las máquinas están paradas, identificar las causas por las que hay bajadas de rendimiento y aumentar el índice de calidad del producto.
Además, hablamos de una herramienta que nos ofrece información fiable en tiempo real del proceso productivo, tanto en relación a la eficiencia de la maquinaria como a la gestión de los recursos humanos.
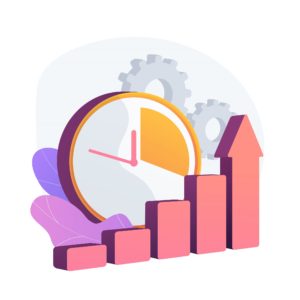
Ejemplo de cálculo del OEE
Para comprender mejor cómo calcular el OEE de una fábrica pondremos un caso práctico. Pongamos por caso que hemos de medir el OEE de una línea de producción durante un turno de 8 horas y con una capacidad productiva de 1.000 piezas/hora.
Ahora, imagina que la línea produce piezas durante sólo 6 horas (disponibilidad del 75%), que produce una media de 700 piezas buenas en una hora (rendimiento del 70%), y que al finalizar el turno ha fabricado 168 piezas defectuosas (calidad del 96%), la fórmula quedaría así:
Disponibilidad 75% * Rendimiento 70% * Calidad 96* = 50,4% de OEE
¿Es suficiente el cálculo del OEE?
Si bien el cálculo del OEE es el punto de partida para medir la productividad de una empresa, se puede dar un paso todavía más ambicioso si nos interesa profundizar en los factores relacionados con las pérdidas de productividad en una fábrica y encontrar la solución adecuada.
Si analizamos el ejemplo anterior, observamos que se han producido 4032 piezas buenas en un turno frente a una capacidad productiva de 8.000 piezas el turno. De este resultado podemos extraer algunas conclusiones:
- Disponibilidad. De 8 horas disponibles solo se ha producido durante 6 horas, debido a paradas pero, ¿cuál es la causa de estos parones? Podría ser desde una dificultad en los tiempos de arranque a una avería.
- Rendimiento. De una capacidad productiva media de 1000 piezas/horas solo se han estado produciendo 700 piezas/horas. Tenemos el dato, pero sería necesario comprender las razones, como microparadas o velocidad de máquina reducida.
- Calidad. Del total de piezas fabricadas cada hora, 168 son defectuosas. Pero, atención, ¿se debe a un error en el proceso productivo o está relacionado, por ejemplo, con el cambio de producto?
Ante unos resultados negativos necesitamos herramientas para identificar las causas de la falta de eficacia como, por ejemplo, la velocidad, las averías, las microparadas, o el cambio de producto. Para ello, hemos querido ir un poco más allá con nuestro sistema MES.
Si deseas obtener una mayor rentabilidad, tomar las medidas oportunas y gestionar tus recursos de forma más eficiente infórmate sobre cómo implantar el sistema MES 4.0 en tu fábrica.