La digitalización y la tecnología están en boca de todos...
La digitalización y la tecnología están en boca de todos, el sector industrial no es una excepción, donde además se reconoce como una gran oportunidad para mejorar la eficiencia de la operaciones en su sentido más amplio: Producción, Productividad, Calidad, Gestión de Almacén, Mantenimiento, Planificación…, no en vano es actualmente el proyecto más estratégico a acometer en el sector industrial, y por ello es el principal destino de las ayudas europeas, estatales y regionales, y cualquier Responsable de Departamento está interesado en el tema. Por otro lado la tecnología forma parte de nuestras vidas: móviles, tablets, PCs, apps, juegos, web en general…, todo instantáneo, a golpe de click, mucha oferta “gratuita”, vamos, que nos parece fácil y, por tanto, lo queremos ya.
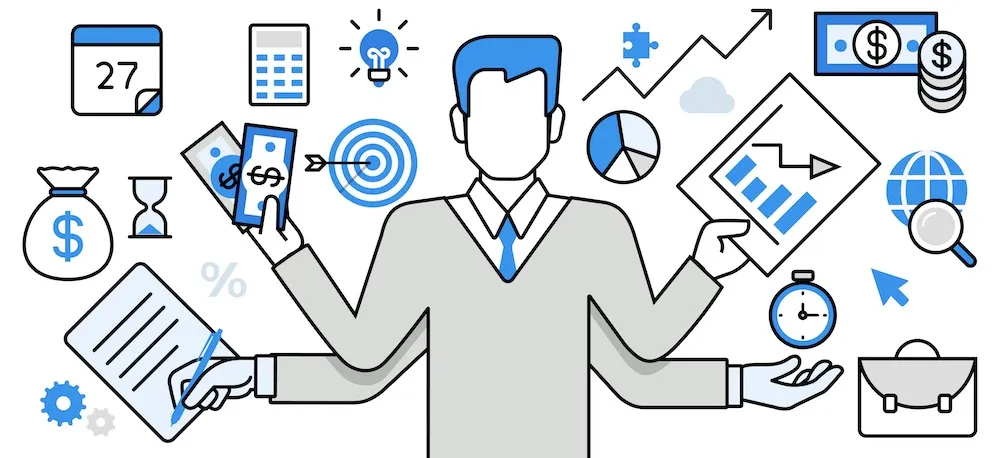
¿Por qué hay entonces tantos proyectos fallidos de Industria 4.0?
La pregunta verbaliza exactamente el sentir del sector y uno de los motivos por el que la industria 4.0 lleva un ritmo de crecimiento demasiado plano. Hay muchas preguntas, mucho interés y todo el mundo tiene claro que la digitalización es el futuro, pero, a la hora de la verdad, aunque las aplicaciones de la industria 4.0 sean muchas, los proyectosno cumplen la expectativas, algo que ocurre en la mayoría de los proyectos, ¿Qué está ocurriendo?
Son muchas cosas y al final se reduce a una sola: la transformación digital de pequeñas y medianas empresas requiere un cambio de paradigma que va más allá de la tecnología (que es condición necesaria, pero claramente insuficiente). El problema está en este punto de partida, en este foco tecnológico junto con un exceso de optimismo o, por qué no, de discursos comerciales sobre dimensionados, por poner un ejemplo: o hablas de predictivos o parece que seas un “pringao”. La realidad es que se está obviando algo fundamental: el Legado, cuya definición tecnológica es software o hardware que es difícil de reemplazar debido a su amplio uso. En el caso del sector industrial esta definición se amplía, identificando 5 capítulos principales: MÁQUINAS, PERSONAS, SISTEMAS, PROCESOS Y CULTURA.
El éxito de los proyectos de Industria 4.0 requiere tener 100% presentes estos “inquilinos” y orientar todas las acciones, tecnológicas y no tecnológicas, a favorecer la transición desde la situación actual a la gestión digital de las fábricas. El éxito de esta tarea requiere de una dirección de proyectos industriales, la de toda la vida: diagnóstico, redacción de un funcional y, por supuesto, Equipo y Plan de proyecto con tareas, hitos, responsables y fechas. La digitalización Industrial va de ganar confianza en base a los hechos y de llegar a resultados concretos, hito a hito, construyendo sobre los logros previos conseguidos. No hay atajos.
Solo así conseguiremos que sean efectivas tecnologías tales como: inteligencia artificial, big data, machine learning, internet de las cosas, edge computing, etc., pero no es posible definir cuándo, estamos demasiado lejos de su aplicación práctica en el sector industrial, no se puede trabajar con datos si no se tienen datos, obvio, ¿no?
1. Resistencia al cambio y aproximación equivocada en la Industria 4.0
Uno de los grandes obstáculos en este tipo de proyectos es la resistencia al cambio y la aproximación equivocada. En MESbook solemos dividirlo en dos posturas comunes que solemos encontrar:
Perspectiva tipo Santo Tomás: el que necesita meter el dedo en la llaga del proyecto y es un escéptico total.
Perspectiva tipo Early Adopter: el que quiere todo cuanto antes y se aproxima a los proyectos de Industria 4.0 desde una perspectiva sobre ilusionada.
La verdad es que los proyectos de la Industria 4.0 requieren huir de las subjetividades que mencionamos anteriormente. No se puede ser demasiado escéptico, porque se entra en la parálisis por análisis, pero tampoco puede ser un “lo quiero todo” y convertirte en un Kamikaze de la digitalización.
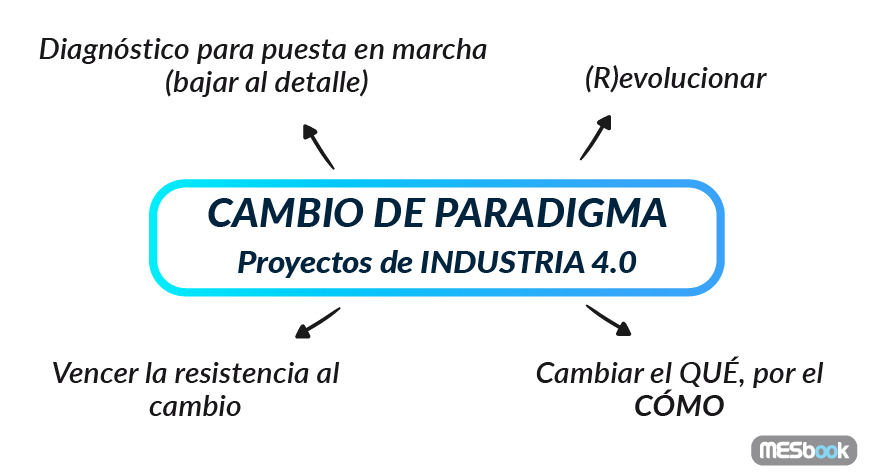
2. En la Digitalización Industrial las cosas no se hacen chasqueando los dedos
Como muchas cosas de nuestra vida, en los proyectos de Industria 4.0 todo parece fácil, hasta que te pones a hacerlo. Es el tipo de escenarios que parecen sencillos, pero donde entra en juego nuestro querido amigo Pareto, el famoso 20%, pero que ocurre todos los días, que nadie ve en el frenesí del hype de la transformación digital y que hace que los proyectos fracasen. Pongamos un ejemplo paralelo de nuestro día a día: Google Maps. ¿Alguien ha pensado en la complejidad que hay detrás de algo que tenemos gratis en nuestros móviles?: mapeo de carreteras, cualquiera, las comarcales también ;), y sus respectivos límites de velocidad, conexión a dispositivos móviles para evaluar el tráfico, mapa de radares, comunicación de radares móviles, acceso a información de incidencias, peajes, toda la algoritmia que hay debajo para calcular la ruta más óptima, recálculos para ofrecer alternativas…seguro que no mencionamos ni una pequeña parte.
Esta imagen nos lleva a entender la complejidad de lo que necesitan las fábricas: que no es ni más ni menos que pasar de conducir la fábrica con papel/excel (mapa de carreteras) a gestionarla digitalmente (Google Maps)
Los proyectos de Industria 4.0 además del análisis profundo que requieren, tienen el agravante de que se tienen que montar sobre recursos ya existentes. Entras en un entorno muy complejo donde hay muchas cosas ya hechas que tienen que seguir funcionando, como las máquinas de todo tipo y antigüedad, los sistemas informáticos como el ERP o procesos como el Sistema de Calidad; pero también otros aspectos que necesitan reinventarse, como los recursos humanos que necesitarán ayuda para salir de la zona de confort, sin duda el mayor reto de la Transformación Digital.
Pongamos otro ejemplo: montar una nueva línea de producción en una fábrica requiere pensar y habilitar el espacio, diseñar e implementar infraestructuras, definir los procesos, formar a los trabajadores, puesta en marcha y múltiples ajustes hasta alcanzar los estándares de Calidad. Nadie en la fábrica es ajeno a esta complejidad, sin embargo las propuestas de Industria 4.0 actuales prácticamente ni las contempla.
La Transformación Digital Industrial es muy compleja y para que las cosas funcionen, para que nos sea útil, debemos tomarnos muy en serio la definición del proyecto de Industria 4.0 bajando al detalle del proceso a mejorar. Hablamos de conectividad en tiempo real, multimáquinas, multipersona, multidispositivo…, e interconexión de todo lo anterior. Debido a esta complejidad y de la necesidad de intervención de múltiples actores internos, fundamental porque serán los futuro usuarios, es clave la figura de un líder interno, con influencia para hacer que las cosas ocurran, un líder de Transformación Digital que dentro de la organización defina, coordine y se asegure el cumplimiento de los hitos de proyecto y el roadmap para la digitalización.
3. En Industria 4.0 nos preguntamos por el QUÉ, pero el CÓMO no siempre está claro.
La digitalización no es un fin en sí mismo, sino un medio para alcanzar un objetivo de eficiencia, y en demasiadas ocasiones el proceso de transformación se queda anclado como el fin a alcanzar. Por esta razón, en Industria 4.0, preguntarse por el QUÉ es sin duda el primer paso y en la mayoría de los casos suele ser muy claro: Ser más eficientes. O si se prefiere: fabricar MÁS, MEJOR y MÁS BARATO. Pero al CÓMO CONSEGUIRLO no se le presta la atención necesaria.
Así que lo primero es hacer un diagnóstico completo y sensato que dé cuenta de los recursos necesarios, pero sobre todo de las estrategias para combatir a los enemigos de la transformación digital. ¿Cuáles son? Ojo que ninguno es tecnológico:
- La resistencia al cambio
- La frustración derivada del sobre compromiso: “No me digas que lo vamos a conseguir mañana, porque a lo mejor me lo creo”.
- Partner inadecuado: Se necesita método y alguien que acompañe en este viaje. Se requiere del “Sherpa de la digitalización” que oriente desde la experiencia y know-how industrial tras cientos de proyectos. El partner debe, como mínimo, hablar el idioma de las fábricas, Por supuesto tener el foco la generación de ahorros tangibles que impacten en el PyG, de lo contrario la Industria 4.0 será irrelevante. Esto nos lleva a una de los mantras de todos los proyectos industriales: PAY BACK y/o el retorno de la inversión. Esto es clave para entender por qué la mayoría de los proyectos son fallidos: no hay retorno, pero es que ni siquiera cumplen los mínimos, como erradicar el papel, y al final la ilusión del inicio desaparece. No se pueder perder de vista en ningún momento la siguiente ecuación: Satisfacción es igual a Resultados menos expectativas.
Como hemos mencionado antes, esto no va sólo de tecnología, aunque ésta es una condición necesaria pero claramente insuficiente. Los principales retos y las razones por las que los proyectos de Industria 4.0 suelen ser fallidos van más allá del ámbito tecnológico. Si estáis pensando en digitalizar vuestra fábrica, es hora de trabajar la resistencia al cambio, en la aproximación que vuestro equipo tiene frente a proyectos de esta envergadura y en el partner que debéis escoger para lograr los resultados deseados.
4. R(evolucionar) la Dirección de proyectos industriales
El éxito de los proyectos de Industria 4.0 requiere una dirección de proyectos industriales asertiva: con diagnósticos, tareas, hitos, responsables y fechas. La digitalización Industrial va de ganar confianza en base a los hechos y consecución de resultados tangibles, requiere de la aplicación de metodologías ágiles/Lean Startup: DEFINE-SAMPLE-TEST-MEASURE, construir sobre QUICK WINS que consiguen debilitar la resistencia al cambio de las organizaciones y están perfectamente identificados: Erradicar el papel, actualización de estándares en BOM/Escandallos y Rutas, Gestión Digital de Calidad, Altas de fabricación y, sobre todo Consumos reales, introducción de rutinas LEAN básicas (TOPx) y primeros Proyectos de Mejora sencillos (no OEE por Velocidad), todos muy “terrenales” pero pasos imprescindibles en el camino de la Transformación Digital, no hay atajos.
COMPARTE ESTE CONTENIDO: