Existen dos formas de hacer crecer tu empresa: aumentando las ventas o reduciendo gastos. Si bien en la mayoría de ocasiones la primera opción centra todos los esfuerzos, lo cierto es que reducir los costes de una empresa industrial es clave para aumentar su competitividad y obtener beneficios.
No se trata de realizar recortes sin ton ni son, sino de actuar con visión estratégica para optimizar los costes, de forma que sea posible producir más gastando menos. Para optimizar los costes de una fábrica será necesario revisar todos los procesos del negocio, desde la tesorería y la fiscalidad a la logística, pasando por el consumo energético.
Por suerte, la tecnología será una gran aliada para optimizar los costes de tu empresa y empezar a crecer. Repasamos 5 consejos para reducir gastos que podrás implantar de inmediato.
Índice
Técnicas para reducir los costes de una empresa industrial
1. Gestión correcta de stocks
Uno de los puntos clave para reducir los costes de una empresa industrial es optimizar el inventario. Para ello, se recomienda buscar el equilibrio entre el coste de inventario y el nivel óptimo de producción para atender a la demanda.
El almacenamiento de la mercancía tras la fabricación comporta gastos derivados del mantenimiento y la logística. Cuando el inventario no se gestiona de forma adecuada pueden darse dos situaciones igualmente perjudiciales: que el capital empleado en la fabricación quede inmovilizado o provocar una rotura de stock sin llegar a satisfacer la demanda.
Una gestión inteligente de tu stock obliga a disponer de herramientas capaces de interpretar los datos de demanda de tus clientes para anticipar la evolución de ventas.
2. Control de los gastos energéticos
La electricidad y los sistemas de climatización pueden suponer un gran desembolso para las fábricas. Por ello, es primordial comparar diferentes ofertas y negociar con las comercializadoras de luz y gas para reducir los costes de una empresa industrial.
Hacer una auditoría para detectar las ineficiencias energéticas ayudará a adoptar medidas de ahorro y a identificar fugas por un inadecuado mantenimiento de las instalaciones.
Además, el incremento del precio de los carburantes y de la electricidad en el momento actual invitan a valorar fuentes alternativas de energía, como la fotovoltaica o la eólica. Encontrar el tipo de energía que mejor se adapta a nuestra actividad productiva ayudará a reducir gastos y a ser más sostenibles. Hecho que puede comportar ventajas fiscales.
3. Eliminar líneas o productos no rentables
Una forma de perder dinero en una empresa industrial es aspirar a ofrecer todo tipo de productos y servicios para llegar a más clientes. Aquellas líneas de negocio o productos que no aportan beneficios conviene eliminarlas para especializarse en aquello que se nos da bien.
Para conseguir una estructura de negocio óptima es recomendable externalizar toda aquella actividad en la que no estéis especializados o que no salga rentable gestionar. Para tomar este tipo de decisiones, por supuesto, se requieren datos y auditorías. Este post sobre cómo se calcula el Oee te puede ser muy útil.
4. Optimizar los gastos de personal
Es importante revisar adecuadamente cuánto gasta tu empresa en personal y tener en cuenta los siguientes aspectos:
- Analizar si puedes aprovechar las nuevas bonificaciones que se dan a la contratación.
- Estudiar la cantidad que se paga por accidente de trabajo y enfermedad profesional.
- Asegurarse de que todos los trabajadores cotizan por la actividad correcta, para evitar sobrecostes.
Por ejemplo, una fábrica con varios centros de trabajo puede tener uno en el que se encuentre su personal estructural o de oficina. Si toda la plantilla cotiza por la actividad principal de la empresa estará pagando de más.
5. Apoyarse en la tecnología
En los proyectos de industria 4.0, disponer de un software de control de producción personalizado es clave para obtener una mayor rentabilidad, disponer de la información para tomar las medidas oportunas y gestionar los recursos de tu empresa de forma más eficiente.
El sistema MESbook permite realizar un control de costes en tiempo real al identificar de manera automática posibles desviaciones de productividad y los motivos que las producen.
MESbook es el único sistema MES que identifica los agujeros de coste en tiempo real. Para ello evalúa desde los costes de mano de obra y de las materias prima, como los diferentes factores de rentabilidad de una fábrica, línea de productos y servicios o clientes.
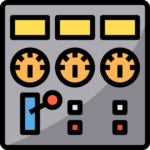
Principales gastos de una empresa industrial
Mantener la actividad de una empresa industrial comporta numerosos gastos, desde los costes de mano de obra y de materias primas hasta gastos de logística o transporte. Entre los diferentes gastos podemos identificar dos tipos: directos e indirectos.
Costes directos de una fábrica
En el caso de las empresas industriales se identifica como costes directos únicamente aquellos que afectan a la producción, es decir, que incurren sobre el proceso productivo. Estos tipos de gasto son principalmente dos: materias primas y mano de obra directa.
¿Cómo nos ayuda implementar el sistema MES a reducir estos gastos?
- Materias primas. Diferencia y cuantifica entre distintos tipos de merma de proceso por precio de compra, de forma que optimiza los costes en materias primas.
- Mano de obra directa. Identifica las causas de la desviación de dinero respecto al estándar de la fábrica, en función del número de personas, la velocidad o el coste por hora trabajada.
Costes industriales indirectos
Los costes indirectos son aquellos que no se relacionan directamente con el proceso productivo, pero que siguen siendo necesarios para la actividad económica de la empresa, como la depreciación, el alquiler de oficinas o plantas de producción, el suministro eléctrico o la mano de obra indirecta.
Tener un registro de distintos tipos de gastos con datos en tiempo real es imprescindible para reducir costes en una empresa industrial y establecer planes de mejora. Solicita información sobre el módulo MES de costes de MESbook. ¡Es el momento de optimizar los costes de tu empresa para empezar a crecer!